Method for producing bamboo board
A production method and bamboo technology, which are used in the pretreatment of molding materials, wood processing appliances, household appliances, etc., can solve the problem that the quality indicators of bamboo boards do not meet the optimal requirements, the specific methods of pressing and molding are not exactly the same, and they cannot fully meet the requirements. Use requirements and other issues, to achieve the effect of simple and easy production process, high production efficiency, and not easy to deform
- Summary
- Abstract
- Description
- Claims
- Application Information
AI Technical Summary
Problems solved by technology
Method used
Image
Examples
Embodiment 1
[0020] 1) adopt commercially available moso bamboo chips, which are processed into silk-connected bamboo chips fragmented along the fiber direction through the rolling and combing of the seaming machine;
[0021] 2) After bleaching, carbonization, and modification treatments, the silk-like bamboo chips are dried or naturally dried to a moisture content of 6%;
[0022] 3) Bamboo slices after step 2) are immersed in melamine resin or phenolic resin adhesive for 360 seconds, taken out and drained vertically, dried or naturally dried to a moisture content of 10%;
[0023] 4) The density of the finished bamboo board is 1.1-1.3g / cm 3 Calculate, take the above-mentioned bamboo chip of corresponding weight, classify by bamboo chip grade, pave and install in the mould, the high grade bamboo chip is used as lining, and the low grade bamboo chip is used as base material;
[0024] 5) Send the paved bamboo chips into the hot press for pressing, the control pressure is 9.5MPa, and the time...
Embodiment 2
[0027] 1) adopt commercially available moso bamboo chips, which are processed into silk-connected bamboo chips fragmented along the fiber direction through the rolling and combing of the seaming machine;
[0028] 2) After bleaching, carbonization and modification treatments, the silk-like bamboo chips are dried or naturally dried to a moisture content of 8%;
[0029] 3) Bamboo slices after step 2) are immersed in melamine resin or phenolic resin adhesive for 420 seconds, taken out and drained vertically, dried or naturally dried to a moisture content of 11%;
[0030] 4) The density of the finished bamboo board is 1.1-1.3g / cm 3 Calculate, take the above-mentioned bamboo chip of corresponding weight, classify by bamboo chip grade, pave and install in the mould, the high grade bamboo chip is used as lining, and the low grade bamboo chip is used as base material;
[0031] 5) Send the paved bamboo chips into the hot press for pressing, the control pressure is 8.5MPa, and the time ...
Embodiment 3
[0034] 1) adopt commercially available moso bamboo chips, which are processed into silk-connected bamboo chips fragmented along the fiber direction through the rolling and combing of the seaming machine;
[0035] 2) After bleaching, carbonization and modification treatment, the silk-like bamboo chips are dried or naturally dried to a moisture content of 10%;
[0036] 3) The bamboo slices in step 2) are immersed in melamine resin or phenolic resin adhesive for 480 seconds, taken out and drained vertically, dried or naturally dried to a moisture content of 12%;
[0037] 4) The density of the finished bamboo board is 1.1-1.3g / cm 3 Calculate, take the above-mentioned bamboo chip of corresponding weight, classify by bamboo chip grade, pave and install in the mould, the high grade bamboo chip is used as lining, and the low grade bamboo chip is used as base material;
[0038] 5) Send the paved bamboo chips into the hot press for pressing, the control pressure is 7.5MPa, and the time...
PUM
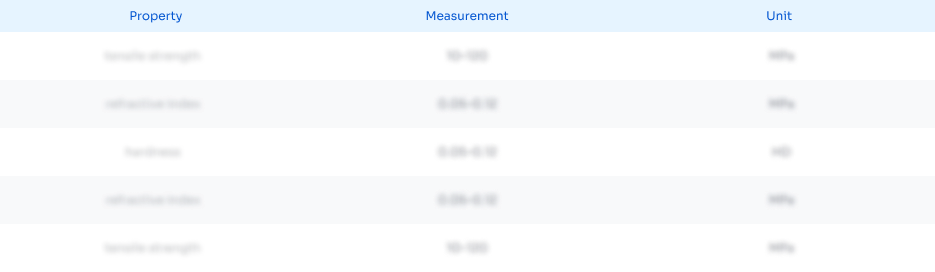
Abstract
Description
Claims
Application Information

- R&D Engineer
- R&D Manager
- IP Professional
- Industry Leading Data Capabilities
- Powerful AI technology
- Patent DNA Extraction
Browse by: Latest US Patents, China's latest patents, Technical Efficacy Thesaurus, Application Domain, Technology Topic, Popular Technical Reports.
© 2024 PatSnap. All rights reserved.Legal|Privacy policy|Modern Slavery Act Transparency Statement|Sitemap|About US| Contact US: help@patsnap.com