Structure of TFT LCD array base plate and manufacturing method of the same
A technology of an array substrate and a manufacturing method, applied to the structure of a TFT LCD array substrate and its manufacturing field, can solve problems such as waste, and achieve the effects of protecting the environment, preventing dust, and reducing emissions
- Summary
- Abstract
- Description
- Claims
- Application Information
AI Technical Summary
Problems solved by technology
Method used
Image
Examples
Embodiment 1
[0031] First of all, using a dedicated film laminating machine, relying on the film laminating roller 3 and atmospheric pressure on it, the polyimide film 2 is evenly pasted on the glass substrate 1 (the glass substrate 1 is placed on the glass substrate conveying roller 4). The method is shown in Figure 4. The specific structure of the cross-section after the polyimide film is pasted is shown in Figure 5. Some polyimide film products have an adhesive coated on one side to help them bond better to the glass substrate.
[0032] Then, a gate metal layer 5 is prepared on the polyimide film 2 by using methods such as sputtering, PECVD, MBE or printing, and its cross-sectional specific structure is shown in FIG. 6 . Then coat the photoresist on the film, and form the required pattern on the photoresist by mask exposure method, wherein the photoresist 6 of the gate part remains, and its cross-sectional specific structure is shown in FIG. 7 . The material area not protected by the ...
Embodiment 2
[0037] First, a layer of water film 14 is formed on the surface of the glass substrate by spraying or sprinkling, as shown in FIG. 9 . The function of the water film 14 is to improve the fluidity of the polyimide film, and remove the air bubbles retained on scratches, trachoma, pits and fabric depressions, thereby improving the flatness and uniformity of the film.
[0038]Then, a polyimide film with a size slightly larger than the glass substrate was placed on the glass substrate with the water film attached, as shown in Figure 10. After the film is positioned correctly, scrape it from the center to both sides with a rake-shaped plastic scraper 15 with a straight rubber end to remove internal air bubbles and moisture, as shown in Figure 11. If there is a local non-fitting place, heat it with a hair dryer to make the film and the glass completely bonded. After checking that there are no bubbles or wrinkles between the polyimide film and the glass substrate, prepare the require...
PUM
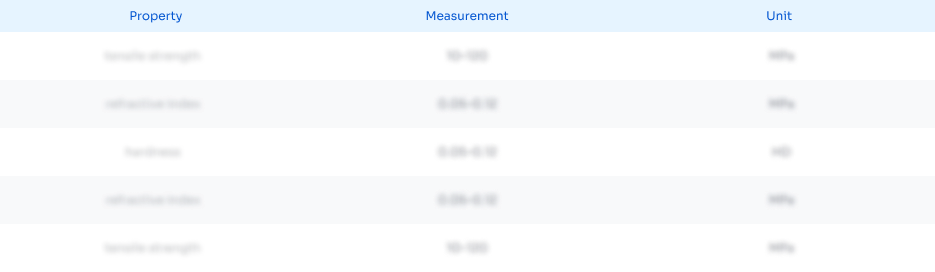
Abstract
Description
Claims
Application Information

- R&D
- Intellectual Property
- Life Sciences
- Materials
- Tech Scout
- Unparalleled Data Quality
- Higher Quality Content
- 60% Fewer Hallucinations
Browse by: Latest US Patents, China's latest patents, Technical Efficacy Thesaurus, Application Domain, Technology Topic, Popular Technical Reports.
© 2025 PatSnap. All rights reserved.Legal|Privacy policy|Modern Slavery Act Transparency Statement|Sitemap|About US| Contact US: help@patsnap.com