Technique of preparing poly lactic acid in use for spinning
A preparation process, polylactic acid technology, applied in the direction of single-component polyester rayon, etc., can solve the problems of high atmosphere environment requirements, low crystallization rate, high thermal shrinkage rate, etc., to reduce production equipment, increase yield, reduce The effect of production energy consumption
- Summary
- Abstract
- Description
- Claims
- Application Information
AI Technical Summary
Problems solved by technology
Method used
Image
Examples
Embodiment 1
[0051] 1. Lactic acid concentration
[0052] Put 300mL of lactic acid into a 1000mL round-bottomed flask, and fix it on a rotary evaporator so that the round-bottomed flask is submerged in a water bath. °C, the vacuum degree is reduced by 10,000Pa, and the evaporation temperature reaches 90°C after 1 hour. When the vacuum degree is reduced by 9,000Pa, the constant temperature concentration is completed after half an hour, and dehydrated concentrated lactic acid is obtained. The yield of concentrated lactic acid reaches 85-91%.
[0053] 2. Precondensation
[0054] Put 220g of concentrated lactic acid into the rotary bottle of rotary film evaporator, add composite catalyst 0.015% HCl, 0.1% tin powder, 0.2% self-made nano-tin powder, and heat up to 180°C at a rate of 1°C per minute in the oil bath , start the vacuum pump, slowly adjust the vacuum degree to 750Pa, polymerize under this condition for 8 hours, cool down to 110°C, and keep the vacuum degree at 80Pa for 2.5 hours to ...
Embodiment 2
[0064] Its concrete preparation method is the same as embodiment 1, and difference is:
[0065] 1. Lactic acid concentration
[0066] Put 300mL of lactic acid into a 1000mL round-bottomed flask, fix it on a rotary evaporator so that the round-bottomed flask is submerged in a water bath, control the temperature at 45°C and the pressure at 70,000Pa, and then increase the temperature by 12°C every half hour. ℃, the vacuum degree is reduced by 15,000Pa, and after 2 hours, the evaporation temperature reaches 85°C, and the vacuum degree is reduced by 10,000Pa, and the concentration is completed after constant temperature for half an hour to obtain dehydrated concentrated lactic acid. The yield of concentrated lactic acid reaches 83-90%.
[0067] 2. Precondensation
[0068] Put 220g of concentrated lactic acid into a rotary bottle, add composite catalyst 0.015% HCl, 0.2% tin powder, 0.1% self-made nano-tin powder, heat up to 170°C at a rate of 2°C per minute in the oil bath, start ...
Embodiment 3
[0075] Its concrete preparation method is the same as embodiment 1, and difference is:
[0076] 1. Lactic acid concentration
[0077] Put 300mL of lactic acid into a 1000mL round-bottomed flask, fix it on a rotary evaporator so that the round-bottomed flask is submerged in a water bath, control the temperature at 55°C and the pressure at 80,000Pa, and increase the temperature by 6 every half hour thereafter. ℃, the vacuum degree is reduced by 14,000Pa. After 2.5 hours, the evaporation temperature reaches 95℃ and the vacuum degree decreases to 12,000Pa. After half an hour of constant temperature, the concentration is completed, and the dehydrated concentrated lactic acid is obtained. The yield of concentrated lactic acid reaches 83-92%.
[0078] 2. Precondensation
[0079] Put 220g of concentrated lactic acid into a rotary bottle, add composite catalyst 0.015% HCl, 0.1% tin powder, 0.2% self-made nano-tin powder, heat up to 190°C at a rate of 3°C per minute in the oil bath, st...
PUM
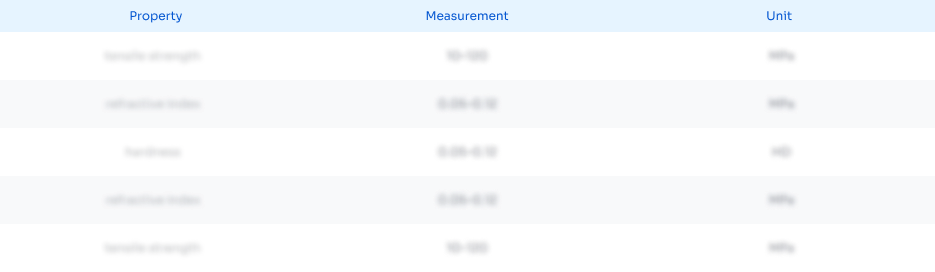
Abstract
Description
Claims
Application Information

- Generate Ideas
- Intellectual Property
- Life Sciences
- Materials
- Tech Scout
- Unparalleled Data Quality
- Higher Quality Content
- 60% Fewer Hallucinations
Browse by: Latest US Patents, China's latest patents, Technical Efficacy Thesaurus, Application Domain, Technology Topic, Popular Technical Reports.
© 2025 PatSnap. All rights reserved.Legal|Privacy policy|Modern Slavery Act Transparency Statement|Sitemap|About US| Contact US: help@patsnap.com