Chloroprene rubber/montmorillonite nano-composite material and its preparation method
A technology of nanocomposite materials and neoprene, which is applied in the field of nanocomposite materials, can solve the problems of intercalation effect nanocomposite performance differences, etc., and achieve good mechanical properties and antistatic properties
- Summary
- Abstract
- Description
- Claims
- Application Information
AI Technical Summary
Problems solved by technology
Method used
Image
Examples
Embodiment 1
[0057] Fully infiltrate 6g of organic montmorillonite with 40ml of toluene, and evenly disperse the montmorillonite in the solvent under magnetic stirring to form A liquid. Dissolve 100g of raw neoprene rubber in 150ml of toluene solvent to form B solution. Mix liquids A and B, stir evenly, heat in a water bath to 95°C, keep the temperature constant, stir, and reflux for 50 hours, heat to separate the solvent, and obtain neoprene raw rubber / montmorillonite nanocomposite. According to the formula shown in Table 1, the composite material is prepared and processed by adopting general-purpose chloroprene rubber mixing, vulcanization methods and techniques (referring to "Modern Rubber Technology", China Petrochemical Press, edited by Yang Qingzhi), to obtain chloroprene rubber / Montmorillonite nanocomposites. Its performance is shown in Table 2 and Table 3.
[0058] sample
Embodiment 2
[0060] Fully infiltrate 4 g of organic montmorillonite with 50 ml of tetrahydrofuran, and uniformly disperse the montmorillonite in the solvent under magnetic stirring, as liquid A. Dissolve 100g of raw neoprene rubber in 200ml of toluene solvent as liquid B.
[0061] Mix liquids A and B, stir evenly, heat in a water bath to 55°C, keep the temperature constant, stir, reflux for 58 hours, heat to separate the solvent, and obtain neoprene raw rubber / montmorillonite nanocomposite. According to the formula shown in Table 1, the composite material is prepared and processed by adopting general-purpose chloroprene rubber mixing, vulcanization methods and techniques (referring to "Modern Rubber Technology", China Petrochemical Press, edited by Yang Qingzhi), to obtain chloroprene rubber / Montmorillonite nanocomposites. Its performance is shown in Table 2 and Table 3.
Embodiment 3
[0063] Fully infiltrate 2-15g organic montmorillonite with 40ml tetrahydrofuran, disperse the montmorillonite evenly in the solvent under magnetic stirring, and use it as liquid A. Dissolve 100g of raw neoprene rubber in 210ml of toluene solvent as solution B.
[0064] Mix liquids A and B, stir evenly, heat in a water bath to 60°C, keep the temperature constant, stir, reflux for 50 hours, heat to separate the solvent, and obtain neoprene raw rubber / montmorillonite nanocomposite. According to the formula shown in Table 1, the composite material is prepared and processed by adopting general-purpose chloroprene rubber mixing, vulcanization methods and techniques (referring to "Modern Rubber Technology", China Petrochemical Press, edited by Yang Qingzhi), to obtain chloroprene rubber / Montmorillonite nanocomposites. Its performance is shown in Table 2 and Table 3.
PUM
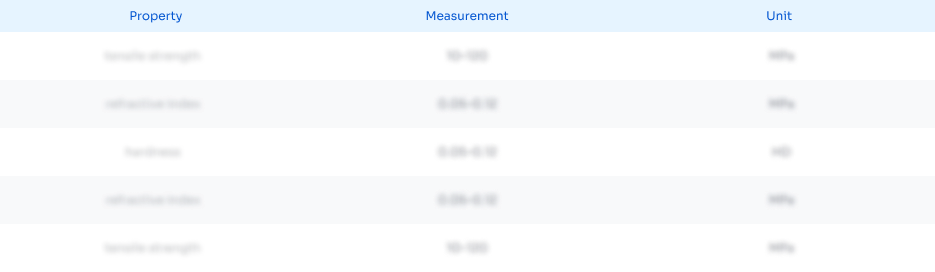
Abstract
Description
Claims
Application Information

- Generate Ideas
- Intellectual Property
- Life Sciences
- Materials
- Tech Scout
- Unparalleled Data Quality
- Higher Quality Content
- 60% Fewer Hallucinations
Browse by: Latest US Patents, China's latest patents, Technical Efficacy Thesaurus, Application Domain, Technology Topic, Popular Technical Reports.
© 2025 PatSnap. All rights reserved.Legal|Privacy policy|Modern Slavery Act Transparency Statement|Sitemap|About US| Contact US: help@patsnap.com