Process for preparing uniform dense orientational poly metal oxide nano film
A nano-film, multi-metal technology, applied in metal material coating process, liquid chemical plating, coating and other directions, can solve the problems of complex device, high substrate requirements, high operating cost, easy operation and equipment requirements. Simple, targeted effects
- Summary
- Abstract
- Description
- Claims
- Application Information
AI Technical Summary
Problems solved by technology
Method used
Image
Examples
Embodiment 1
[0021] Step A: take by weighing 38.68g Ni(NO 3 ) 2 ·6H 2 O and 24.99g Al(NO 3 ) 3 9H 2 O dissolved in 250mL to remove CO 2 In the water, prepare a mixed salt solution, another 15.20g NaOH is dissolved in 250mL to remove CO 2 At room temperature, quickly pour the alkali solution and the mixed salt solution into the fully back-mixed rotary liquid film reactor to react for 1min, and the obtained slurry was heated at 100°C under N 2 Crystallize under protection for 8 hours, centrifuge, wash to neutral, weigh a certain amount of product to prepare 10mL aqueous solution with a concentration of 4.3wt%, stir evenly at room temperature, pour into a petri dish with a diameter of 90mm, and store at 20°C Drying for 4 days, you can get NiAl-NO 3 LDHs precursor, its Ni 2+ / Al 3+ =2.
[0022] Step B: NiAl-NO obtained in step A 3 The LDHs precursor was placed in a muffle furnace at 900 °C for 2 hours to obtain NiAl-MMO 900 nano film.
[0023]The resulting NiAl-MMO 900 The XRD sp...
Embodiment 2
[0025] Step A: take by weighing 38.68g Ni(NO 3 ) 2 ·6H 2 O and 26.91g Fe(NO 3 ) 3 9H 2 O dissolved in 250mL to remove CO 2 In the water, prepare a mixed salt solution, another 15.20g NaOH is dissolved in 250mL to remove CO 2 At room temperature, quickly pour the alkali solution and the mixed salt solution into the fully back-mixed rotary liquid film reactor to react for 1min, and the obtained slurry was heated at 100°C under N 2 Crystallize under protection for 8 hours, centrifuge, wash to neutral, weigh a certain amount of product to prepare 10mL aqueous solution with a concentration of 5wt%, stir evenly at room temperature, pour it into a petri dish with a diameter of 90mm, and store it at 40°C Dry for 8 hours to get NiFe-NO 3 LDHs precursor, its Ni 2+ / Fe 3+ =2.
[0026] Step B: NiFe-NO obtained in step A 3 The LDHs precursor was placed in a muffle furnace at 1000 °C for 24 hours to obtain NiFe-MMO 1000 nano film.
[0027] Via NiFe-MMO 1000 The XRD and SEM cha...
Embodiment 3
[0029] Step A: take by weighing 28.56g Zn(NO 3 ) 2 ·6H 2 O and 18.01g Al(NO 3 ) 3 9H 2 O dissolved in 150mL to remove CO 2 In the water, it is prepared as a mixed salt solution, and another 9.12g NaOH is dissolved in 150mL to remove CO 2 At room temperature, quickly pour the alkali solution and the mixed salt solution into the fully back-mixed rotary liquid film reactor to react for 1min, and the obtained slurry was heated at 100°C under N 2 Crystallize under protection for 8 hours, centrifuge, wash to neutral, weigh a certain amount of product to prepare 10mL aqueous solution with a concentration of 3.6wt%, stir evenly at room temperature, pour into a petri dish with a diameter of 90mm, and store at 50°C Dry for 6 hours to get ZnAl-NO 3 LDHs precursor, its Zn 2+ / Al 3+ =2.
[0030] Step B: the ZnAl-NO obtained in step A 3 The LDHs precursor was placed in a muffle furnace and calcined at 500 °C for 15 min to obtain ZnAl-MMO 500 nano film.
[0031] by ZnAl-MMO 500...
PUM
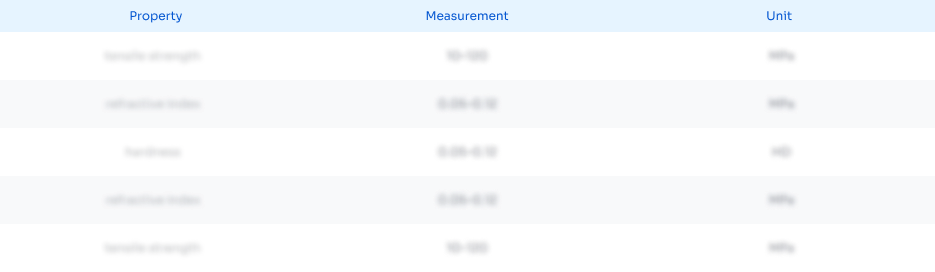
Abstract
Description
Claims
Application Information

- Generate Ideas
- Intellectual Property
- Life Sciences
- Materials
- Tech Scout
- Unparalleled Data Quality
- Higher Quality Content
- 60% Fewer Hallucinations
Browse by: Latest US Patents, China's latest patents, Technical Efficacy Thesaurus, Application Domain, Technology Topic, Popular Technical Reports.
© 2025 PatSnap. All rights reserved.Legal|Privacy policy|Modern Slavery Act Transparency Statement|Sitemap|About US| Contact US: help@patsnap.com