Method of preparing pentafluoroethane
A manufacturing method and technology of pentafluoroethane, applied in the direction of halogen substitution preparation, organic chemistry, etc., can solve the problems of low conversion rate of HCFC-133a and low selectivity of HCFC-123, achieve reduced catalyst poisoning, high catalyst activity, and reduced replacement or the effect of regeneration frequency
- Summary
- Abstract
- Description
- Claims
- Application Information
AI Technical Summary
Problems solved by technology
Method used
Image
Examples
Embodiment
[0082] Tests were conducted on the reaction steps (a) and (b) in the production method of the present invention.
[0083] (Test 1) Reaction process (b) (1st reaction process)
[0084] A tubular nickel reaction tube having an inner diameter of 2 mm and a length of 12.1 m was maintained under the conditions of about 0.6 MPa and various temperatures shown in Table 1 . HCFC-133a and Cl preheated to about 200°C are made at flow rates of 180cc / min and 30cc / min respectively 2 into the above reaction tube.
[0085] Wash the reaction product (gas mixture) coming out of the reaction tube with a dilute alkaline aqueous solution warmed to 70°C in advance to remove HCl and Cl 2 . The composition of the mixture thus obtained was analyzed by gas chromatography with a hydrogen flame ionization detector (FID), and the conversion rate of HCFC-133a, the selectivity of HCFC-123 to CFC-113a, and the HCFC-1326 in the mixture were determined. concentration. In addition, the selectivity of HCFC-...
PUM
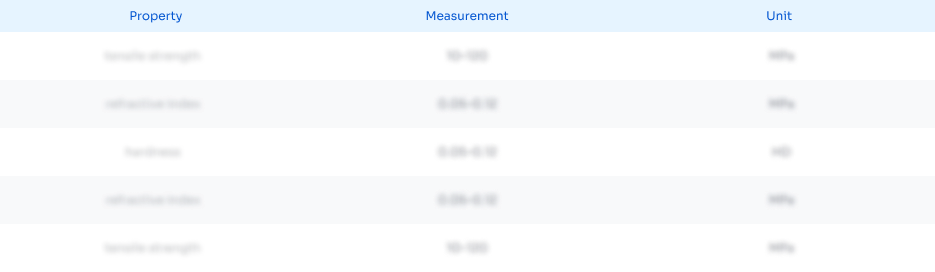
Abstract
Description
Claims
Application Information

- R&D
- Intellectual Property
- Life Sciences
- Materials
- Tech Scout
- Unparalleled Data Quality
- Higher Quality Content
- 60% Fewer Hallucinations
Browse by: Latest US Patents, China's latest patents, Technical Efficacy Thesaurus, Application Domain, Technology Topic, Popular Technical Reports.
© 2025 PatSnap. All rights reserved.Legal|Privacy policy|Modern Slavery Act Transparency Statement|Sitemap|About US| Contact US: help@patsnap.com