Method of on-line pretreatment inhibiting coking by hydrocarbon pyrolysis apparatus
A cracking device and pretreatment technology, applied in cracking, non-catalytic thermal cracking, petroleum industry and other directions, can solve the problems of carburizing the inner wall of the furnace tube, carburizing the furnace tube, uneconomical, etc. Erosion resistance and improved service life
- Summary
- Abstract
- Description
- Claims
- Application Information
AI Technical Summary
Problems solved by technology
Method used
Image
Examples
Embodiment Construction
[0033] Further illustrate content of the present invention below in conjunction with example, but this example does not limit protection scope of the present invention.
[0034] The examples show a comparison of coated samples and uncoated tests in a home-made laboratory setup. The schematic diagram of the cracking test device is shown in Figure 1.
[0035] The heating furnace is a two-stage temperature-controlled tubular heating furnace with a heating length of 1000mm; the cracking tube is an HK40 tube with an outer diameter of 25mm and a length of 200mm, and the length of the preheating part of the front section is 1m. When pretreating the cracking tube, sulfur and silicon-containing compounds enter the cracking furnace tube along with water vapor to deposit sulfur and silicon dioxide composite coating, using carbon disulfide and tetramethoxysilane. Among them, the ratio of sulfur to silicon atoms is 2:1, the ratio of silicon compound to water vapor is 2.4g / h, and the flow ...
PUM
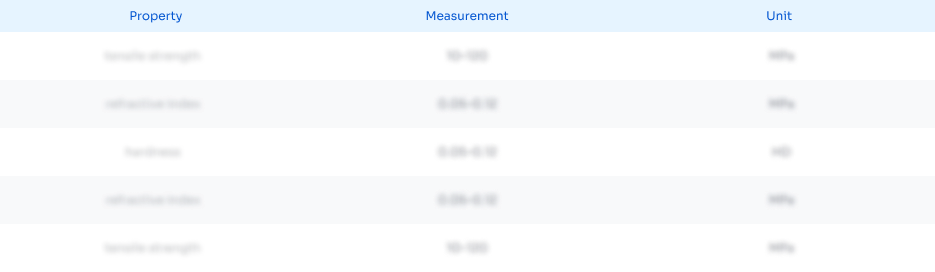
Abstract
Description
Claims
Application Information

- R&D Engineer
- R&D Manager
- IP Professional
- Industry Leading Data Capabilities
- Powerful AI technology
- Patent DNA Extraction
Browse by: Latest US Patents, China's latest patents, Technical Efficacy Thesaurus, Application Domain, Technology Topic, Popular Technical Reports.
© 2024 PatSnap. All rights reserved.Legal|Privacy policy|Modern Slavery Act Transparency Statement|Sitemap|About US| Contact US: help@patsnap.com