Manufacture method of linear low density polyethylene lawn-shape ground cushion
A linear low density, polyethylene technology for use in the direction of household components, applications, home appliances
- Summary
- Abstract
- Description
- Claims
- Application Information
AI Technical Summary
Problems solved by technology
Method used
Image
Examples
Embodiment 1
[0027] The linear low-density polyethylene (LLDPE, 7047) is used as raw material, and industrial pigment (reduced bright green FFB) is added, and the added amount accounts for 0.8% of the linear low-density polyethylene (LLDPE) according to the weight percentage.
[0028] The processing steps are as follows:
[0029] The raw materials are stirred, and the raw materials are respectively added into a high-speed mixer, stirred and mixed, and the stirring speed is 5000 rpm, and the time is 50 minutes.
[0030] High temperature and high pressure injection molding. Put the mixed raw materials into a high-temperature and high-pressure injection molding machine, and perform injection molding at a temperature of 180° C. and a pressure of 2 MPa.
[0031] Injection molding. The injection molding material is added to the mold cast according to the shape of the product, and is shaped by the mold.
[0032] Composite, bonding non-woven fabric and heat-resistant non-slip mesh on the bottom...
Embodiment 2
[0037] The linear low-density polyethylene (LLDPE, 7540) is used as raw material, and industrial pigment (reduced olive green B) is added, and the added amount accounts for 0.01% of the linear low-density polyethylene (LLDPE) according to the weight percentage.
[0038] The processing steps are as follows:
[0039] The raw materials are stirred, and the raw materials are respectively added into a high-speed mixer, stirred and mixed, and the stirring speed is 1000 rpm, and the time is 150 minutes.
[0040] High temperature and high pressure injection molding. Put the mixed raw materials into a high-temperature and high-pressure injection molding machine, and perform injection molding at a temperature of 170° C. and a pressure of 0.5 MPa.
[0041] Injection molding. The injection molding material is added to the mold cast according to the shape of the product, and is shaped by the mold.
[0042] Composite, bonding non-woven fabric and heat-resistant non-slip mesh on the botto...
Embodiment 3
[0047] The linear low-density polyethylene (LLDPE, 7042) is used as a raw material, and an industrial pigment (phthalocyanine green G) is added, and the added amount accounts for 2% of the linear low-density polyethylene (LLDPE) according to the weight percentage.
[0048] The processing steps are as follows:
[0049] The raw materials are stirred, and the raw materials are respectively added into a high-speed mixer, and stirred and mixed at a stirring rate of 10000 rpm for 5 minutes.
[0050] High temperature and high pressure injection molding. Put the mixed raw materials into a high-temperature and high-pressure injection molding machine, and inject them under the conditions of a temperature of 190° C. and a pressure of 5 MPa.
[0051] Injection molding. The injection molding material is added to the mold cast according to the shape of the product, and is shaped by the mold.
[0052] Composite, bonding non-woven fabric and heat-resistant non-slip mesh on the bottom surfa...
PUM
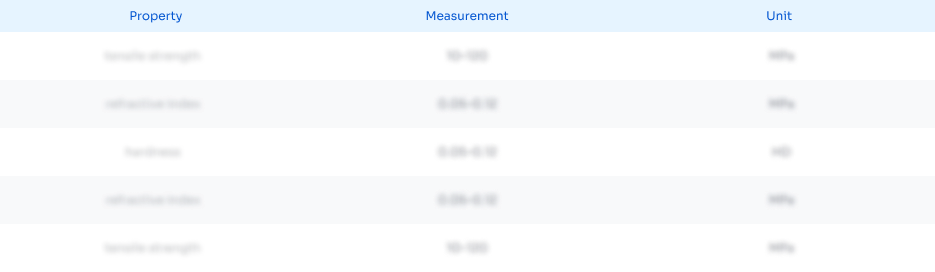
Abstract
Description
Claims
Application Information

- R&D Engineer
- R&D Manager
- IP Professional
- Industry Leading Data Capabilities
- Powerful AI technology
- Patent DNA Extraction
Browse by: Latest US Patents, China's latest patents, Technical Efficacy Thesaurus, Application Domain, Technology Topic, Popular Technical Reports.
© 2024 PatSnap. All rights reserved.Legal|Privacy policy|Modern Slavery Act Transparency Statement|Sitemap|About US| Contact US: help@patsnap.com