Method for producing light-pollution reverse osmosis composite film
A reverse osmosis membrane and production method technology, applied in the field of water treatment, can solve problems such as difficult operation, high degree of saponification, loss of protective layer, etc., and achieve improved pollution resistance, improved hydrophilicity, high desalination rate and water flow volume effect
- Summary
- Abstract
- Description
- Claims
- Application Information
AI Technical Summary
Problems solved by technology
Method used
Examples
Embodiment 1
[0014] The production method of low-pollution composite reverse osmosis membrane comprises the following steps:
[0015] (1) Preparation of A solution: Dissolve 2.5 kg of m-phenylenediamine and 0.5 kg of sodium lauryl sulfate in 97.0 kg of water, and stir to obtain A solution.
[0016] (2) Preparation of solution B: 0.1 kg of trimesoyl chloride was dissolved in 100 kg of naphtha (Naphtha, Shell Chemicals) to obtain solution B.
[0017] (3) Preparation of solution C: 2kg of polyvinyl alcohol (PVA) with an average degree of polymerization of 1000 (n=1000) and a degree of saponification of 75% is dissolved in 97.7kg of hot water at 60°C, and after fully stirring for 10 minutes , then add 0.2kg of glutaraldehyde and 0.1kg of hydrochloric acid, and continue to stir for 30 minutes to fully react to form a C solution.
[0018] (4) Coating solution A on the polysulfone support layer, removing excess solution A, and then contacting the support layer with solution B to form a polyamide...
Embodiment 2
[0021] The production method of low-pollution composite reverse osmosis membrane comprises the following steps:
[0022] (1) Preparation of A solution: Dissolve 2.5 kg of m-phenylenediamine and 0.5 kg of sodium dodecylbenzenesulfonate in 97.0 kg of water, and stir to obtain A solution.
[0023] (2) The preparation of B solution: with embodiment 1.
[0024] (3) Preparation of solution C: 2kg of polyvinyl alcohol (PVA) with an average degree of polymerization of 500 (n=500) and a degree of saponification of 75% is dissolved in 97.7kg of hot water at 60°C, and after fully stirring for 10 minutes , then add 0.2kg of melamine and 0.1kg of hydrochloric acid, and continue to stir for 30 minutes to fully react to form a C solution.
[0025] Remaining steps are with embodiment 1.
[0026] The contact angle was measured to be 21°. Then adopt the same test method as Example 1, and the obtained results are shown in Table 1.
Embodiment 3
[0028] The production method of low-pollution composite reverse osmosis membrane comprises the following steps:
[0029] (1) Preparation of A solution: Dissolve 2.5 kg of m-phenylenediamine and 0.5 kg of N-methylpyrrolidone in 97.0 kg of water, and stir to obtain A solution.
[0030] (2) Preparation of B solution: same as in Example 1.
[0031] (3) Preparation of solution C: 2kg of polyvinyl alcohol (PVA) with an average degree of polymerization of 1000 (n=1000) and a degree of saponification of 75% is dissolved in 97.7kg of hot water at 60°C, and after fully stirring for 10 minutes , then add 0.2kg of glyoxal and 0.1kg of hydrochloric acid, and continue to stir for 30 minutes to fully react to form a C solution.
[0032] Remaining steps are with embodiment 1.
[0033] The contact angle was measured to be 20°. Then adopt the same test method as Example 1, and the obtained results are shown in Table 1.
PUM
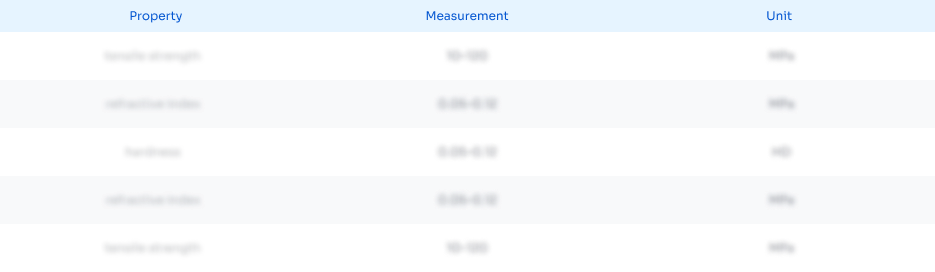
Abstract
Description
Claims
Application Information

- R&D
- Intellectual Property
- Life Sciences
- Materials
- Tech Scout
- Unparalleled Data Quality
- Higher Quality Content
- 60% Fewer Hallucinations
Browse by: Latest US Patents, China's latest patents, Technical Efficacy Thesaurus, Application Domain, Technology Topic, Popular Technical Reports.
© 2025 PatSnap. All rights reserved.Legal|Privacy policy|Modern Slavery Act Transparency Statement|Sitemap|About US| Contact US: help@patsnap.com