Method for producing diethylbenzene through dehydrogenation of diethyl benzene
A divinylbenzene and diethylbenzene technology, applied in the field of diethylbenzene dehydrogenation to prepare divinylbenzene, can solve the problems of low yield of diethylbenzene dehydrogenation products, chromium pollution, etc., achieve high anti-coking ability, high The effect of selectivity, good technical effect
- Summary
- Abstract
- Description
- Claims
- Application Information
AI Technical Summary
Problems solved by technology
Method used
Image
Examples
Embodiment 1
[0022] Combine 185 grams of iron oxide red, 120 grams of iron oxide yellow, 65 grams of potassium carbonate, 60 grams of cerium nitrate, 20 grams of praseodymium nitrate, 9.5 grams of ammonium molybdate, 30 grams of calcium oxalate, 2.1 grams of vanadium oxide, 2 grams of manganese oxide, 2.3 G tin oxide, 0.4 g boron oxide, 10 g carboxymethyl cellulose are mixed uniformly, 140 g deionized water is added, the wet material is kneaded into a dough suitable for extruding, extruding, cutting into pellets, and aging at room temperature for 10 hours. Put it into an oven, dry at 80°C for 6 hours, put it in a roasting furnace, and roast at 800°C for 2 hours to obtain a finished catalyst. Load 100 ml of catalyst into the evaluation reactor. At the reaction temperature of 620°C, the weight ratio of water / diethylbenzene is 2.0:1, the pressure is 50KPa, and the space velocity is 0.05 hours. -1 Catalytic activity is evaluated under the conditions, and the qualification rate of boiling water tes...
Embodiment 2
[0024] Load 100 ml of the catalyst of Example 1 into the evaluation reactor. At the reaction temperature of 580°C, the weight ratio of water / diethylbenzene is 4.5:1, the pressure is 30KPa, and the space velocity is 0.1 hour. -1 Catalytic activity is evaluated under the conditions, and the qualification rate of boiling water test and cold water test are determined. Test results: the conversion rate of diethylbenzene was 80.9%, the selectivity of stilbene was 52.0%, the selectivity of ethyl styrene was 34.1%, the boiling water test was qualified, and the cold water test was qualified.
Embodiment 3
[0026] Load 100 ml of the catalyst of Example 1 into the evaluation reactor at a reaction temperature of 640°C, a weight ratio of water / diethylbenzene of 3.0:1, normal pressure, and a space velocity of 0.3 hours. -1 Catalytic activity is evaluated under the conditions, and the qualification rate of boiling water test and cold water test are determined. Test results: the conversion rate of diethylbenzene is 80.6%, the selectivity of stilbene is 52.3%, the selectivity of ethyl styrene is 34.3%, the boiling water test is qualified, and the cold water test is qualified.
PUM
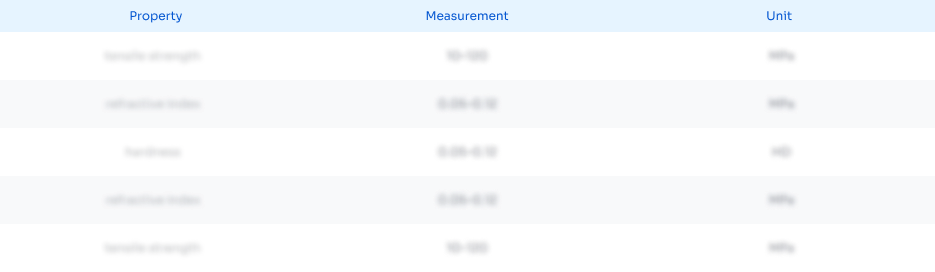
Abstract
Description
Claims
Application Information

- R&D Engineer
- R&D Manager
- IP Professional
- Industry Leading Data Capabilities
- Powerful AI technology
- Patent DNA Extraction
Browse by: Latest US Patents, China's latest patents, Technical Efficacy Thesaurus, Application Domain, Technology Topic, Popular Technical Reports.
© 2024 PatSnap. All rights reserved.Legal|Privacy policy|Modern Slavery Act Transparency Statement|Sitemap|About US| Contact US: help@patsnap.com