Porous fiber modified concrete
A porous fiber and concrete technology, applied in the field of concrete or mortar, can solve the problems of poor tensile and toughness and other mechanical properties, high brittleness and easy cracking, etc., to reduce the possibility of cracking, improve impact resistance, and enhance the effect of toughness.
- Summary
- Abstract
- Description
- Claims
- Application Information
AI Technical Summary
Problems solved by technology
Method used
Examples
Embodiment 1
[0034] Example 1: Contrastive experiment of improving the fireproof and anti-explosion performance of concrete
[0035] In order to verify the fire and explosion protection effect of porous fiber concrete, comparative experiments were carried out on ordinary concrete and porous fiber concrete, the situation is as follows:
[0036] Specimen 1: Ordinary concrete specimen
[0037] 1) Concrete grade C25.
[0038] 2) The concrete mix ratio refers to the "Ordinary Concrete Mix Ratio Design Regulations, JGJ55-2000", without other admixtures.
[0039] 3) The test was carried out after a curing period of 28 days.
[0040] 4) Mixing system: dry mix fine aggregate + cement + fiber + coarse aggregate for 1 minute, add water and then wet mix for 2 minutes.
[0041] Specimen 2: Porous fiber concrete specimen
[0042] 1) The mix ratio of concrete is the same as above;
[0043] 2) Add polypropylene porous fibers with a dosage of 2kg / m3 into the concrete.
[0044] 3) Stirring system: the...
Embodiment 2
[0047] Embodiment 2: Comparative experiment of anti-shrinkage performance
[0048] In order to verify the anti-crack and anti-seepage effect of porous fiber concrete, comparative experiments were carried out on ordinary concrete and porous fiber concrete, the situation is as follows:
[0049] Specimen 1: Ordinary concrete specimen
[0050] 4) Concrete grade C25.
[0051] 5) Concrete mix ratio refers to "Common Concrete Mix Ratio Design Regulations, JGJ55-2000", without other admixtures.
[0052] 6) Mixing system: dry mix fine aggregate + cement + fiber + coarse aggregate for 1 minute, add water and then wet mix for 2 minutes.
[0053] Specimen 2: Porous fiber concrete specimen
[0054] 1) The mixing ratio and mixing process of concrete are the same as above.
[0055] 2) Add 2kg / m to the concrete 3porous polypropylene fibers.
[0056] 3) Stirring system: appropriately prolong the stirring time to make the fibers disperse evenly.
[0057] The experimental process was carr...
PUM
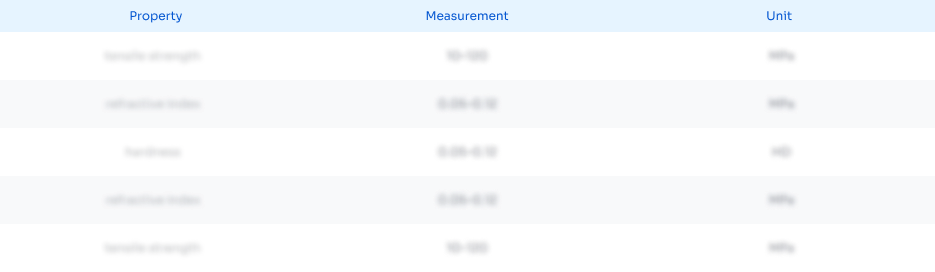
Abstract
Description
Claims
Application Information

- R&D
- Intellectual Property
- Life Sciences
- Materials
- Tech Scout
- Unparalleled Data Quality
- Higher Quality Content
- 60% Fewer Hallucinations
Browse by: Latest US Patents, China's latest patents, Technical Efficacy Thesaurus, Application Domain, Technology Topic, Popular Technical Reports.
© 2025 PatSnap. All rights reserved.Legal|Privacy policy|Modern Slavery Act Transparency Statement|Sitemap|About US| Contact US: help@patsnap.com