Method for simultaneously removing multiple harmful impurity from coal gas
A technology for removing impurities, applied in separation methods, chemical instruments and methods, and purification of combustible gases, etc., can solve problems such as inability to meet the purification requirements of chemical production, high investment in step-by-step treatment devices, and high operating costs for multi-stage purification. , to achieve the effects of small footprint, low labor intensity and easy operation
- Summary
- Abstract
- Description
- Claims
- Application Information
AI Technical Summary
Problems solved by technology
Method used
Examples
Embodiment 1
[0026] A steel company 22000Nm 3 / h coke oven gas purification device
[0027] Impurities
[0028] name
[0029] 3. Adsorption parameters
[0030] 3.1 Adsorption tower φ3600×9320 4 sets
[0031] 3.2 Adsorbent coke, silica gel, iron oxide desulfurizer, modified activated carbon, alumina and
[0032] Composition of ceramic balls
[0033] 3.3 Filling parameters Number of filling layers 6 layers
[0034] The total height of filling is 5.82 meters
[0035] 4. Regeneration parameter Regeneration temperature 360~450℃
[0036] Regeneration pressure 0.015MPa
[0037] Carrier Gas Composition Steam
[0038] The regeneration cycle is 45 days.
[0039] 5. Purification result
[0040] Impurities
[0041] name
Embodiment 2
[0043] A steel company 15000Nm 3 / h coke oven gas purification device
[0044] Impurities
[0045] name
[0046] 3. Adsorption parameters
[0047] 3.1 Adsorption tower φ3200×15120 6 sets
[0048] 3.2 Adsorbent coke, 5A molecular sieve, swamp iron ore and diatomite molding, activated carbon, iron
[0049] Composition of manganese zinc desulfurizer, alumina, 10A molecular sieve and ceramic ball
[0050] 3.3 Filling parameters Loading layers 8 layers
[0051] The total height of filling is 12.5 meters
[0052] 4. Regeneration parameter Regeneration temperature 300~450℃
[0053] Regeneration pressure 0.015MPa
[0054] Carrier Gas Composition Steam
[0055] The regeneration cycle is 90 days.
[0056] 5. Purification result
[0057] Impurities
[0058] name
PUM
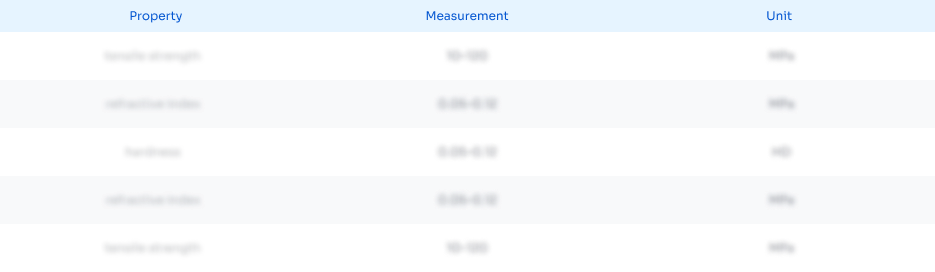
Abstract
Description
Claims
Application Information

- R&D
- Intellectual Property
- Life Sciences
- Materials
- Tech Scout
- Unparalleled Data Quality
- Higher Quality Content
- 60% Fewer Hallucinations
Browse by: Latest US Patents, China's latest patents, Technical Efficacy Thesaurus, Application Domain, Technology Topic, Popular Technical Reports.
© 2025 PatSnap. All rights reserved.Legal|Privacy policy|Modern Slavery Act Transparency Statement|Sitemap|About US| Contact US: help@patsnap.com