Method of preparing organic molecular alloy phase change energy storage material
A technology of energy storage materials and organic molecules, applied in heat exchange materials, chemical instruments and methods, instruments, etc., can solve problems such as low density, aging, and small thermal conductivity
- Summary
- Abstract
- Description
- Claims
- Application Information
AI Technical Summary
Problems solved by technology
Method used
Image
Examples
Embodiment 1
[0017] Use chemically pure n-octanoic acid and lauric acid as raw materials. Set the test ratio (molar ratio) series as n-octanoic acid: lauric acid=5:95, 10:90, 15:85, 20:80, 25:75, 30:70, 35:65, 40:60, 45 : 55, 50: 50, 55: 45, 60: 40, 65: 35, 70: 30, 75: 25, 80: 20, 85: 15, 90: 10, 95: 5. Keep the test mixture in a constant temperature and heat preservation container at 80°C for 4 hours, then put the test tube into the water bath of the ultrasonic generator, control the temperature of the water bath to 60°C, the ultrasonic vibration time for 3 minutes, and the ultrasonic frequency for 40-50 Kilohertz. After the thermal analysis test of the above-mentioned series of trial mixes, the trial mix with single phase transition temperature and maximum phase transition heat is taken, and the target ratio is determined to be n-octanoic acid: lauric acid = 80:20 (molar ratio). See the DSC test results of the alloy figure 1 .
Embodiment 2
[0019] Use chemically pure n-octanoic acid and palmitic acid as raw materials. Set the trial ratio (molar ratio) series as n-octanoic acid: palmitic acid=5:95, 10:90, 15:85, 20:80, 25:75, 30:70, 35:65, 40:60, 45 : 55, 50: 50, 55: 45, 60: 40, 65: 35, 70: 30, 75: 25, 80: 20, 85: 15, 90: 10, 95: 5. Keep the test mixture in a constant temperature and heat preservation container at 90℃ for 2.5 hours, then put the test tube into the water bath of the ultrasonic generator, control the temperature of the water bath to 50℃, the ultrasonic vibration time for 5 minutes, and the ultrasonic frequency for 40-50 Kilohertz. After the thermal analysis test of the above-mentioned series of trial mixes, the trial mix with single phase transition temperature and maximum phase transition heat is taken, and the target ratio is determined to be n-octanoic acid: palmitic acid = 95: 5 (molar ratio). See the DSC test results of the alloy figure 2 .
Embodiment 3
[0021] Use chemically pure capric acid and myristic acid as raw materials. Set the test ratio (molar ratio) series as capric acid: myristic acid = 5: 95, 10: 90, 15: 85, 20: 80, 25: 75, 30: 70, 35: 65, 40: 60, 45:55, 50:50, 55:45, 60:40, 65:35, 70:30, 75:25, 80:20, 85:15, 90:10, 95:5. Keep the test mixture in a constant temperature and heat preservation container at 100°C for 1 hour, then put the test tube into the water bath of the ultrasonic generator, control the temperature of the water bath to 80°C, the ultrasonic vibration time for 1 minute, and the ultrasonic frequency for 40-50 Kilohertz. After the thermal analysis test of the above-mentioned series of trial mixes, the trial mix with single phase transition temperature and maximum phase transition heat is taken, and the target mix ratio is determined to be capric acid: myristic acid = 75: 25 (molar ratio). See the DSC test results of molecular alloys image 3 .
[0022] From the above examples and the DSC test results of or...
PUM
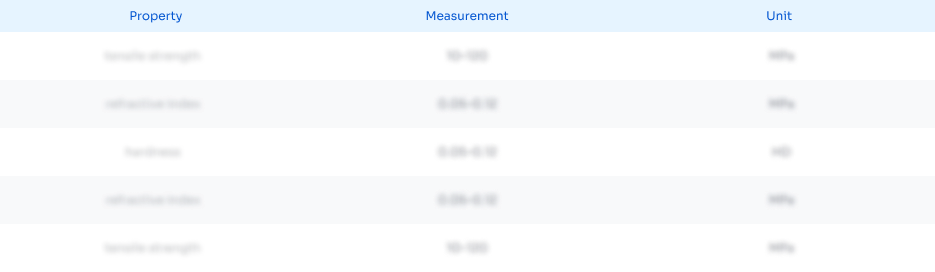
Abstract
Description
Claims
Application Information

- R&D Engineer
- R&D Manager
- IP Professional
- Industry Leading Data Capabilities
- Powerful AI technology
- Patent DNA Extraction
Browse by: Latest US Patents, China's latest patents, Technical Efficacy Thesaurus, Application Domain, Technology Topic, Popular Technical Reports.
© 2024 PatSnap. All rights reserved.Legal|Privacy policy|Modern Slavery Act Transparency Statement|Sitemap|About US| Contact US: help@patsnap.com