High polymer composite material manhole lid and its production method
A composite material and polymer technology, applied in the field of polymer composite material manhole cover and its manufacturing, can solve the problems of high market price of hard rubber and heavy calcium powder, the bearing capacity cannot meet the requirements, and the production cost of the manhole cover is affected. The effect of high strength, improved bearing capacity, and high thermal stability
- Summary
- Abstract
- Description
- Claims
- Application Information
AI Technical Summary
Problems solved by technology
Method used
Image
Examples
Embodiment 1
[0038] 1. Preparation of materials:
[0039] At room temperature, pour 45% to 70% of coal ash and 5% to 15% of polymer unsaturated resin into the mixer, stir for 3 to 6 minutes, add 15% to 30% of fiber, and stir together for 1 to 4 minutes. minute. Then add the mixture of curing agent, defoamer, reinforcing agent, zinc stearate and pigment, and stir for 2 to 5 minutes to fully mix the raw materials.
[0040] 2. Filling:
[0041] First smear or evenly spray the release agent on the mold, pour 30% to 60% of the raw material mixture into the mold cavity, put the T-shaped steel skeleton, and then pour the remaining raw material mixture.
[0042] 3. Compression molding:
[0043] After all the raw material mixture is added to the mold cavity, close the mold, control the pressure within the range of 200-300 tons, control the temperature within the range of 100-150°C, keep it for 8-15 minutes, then open the mold and eject it.
Embodiment 2
[0045] 1. Material preparation: At room temperature, pour 60% coal ash and 15% polymer unsaturated resin into the mixer, stir for 4 minutes, add 15% fiber, and stir together for 3 minutes. Then add the mixture of curing agent, defoamer, reinforcing agent, zinc stearate and pigment, and stir for 4 minutes to fully mix the raw materials.
[0046] 2. Filling:
[0047] Smear or evenly spray the release agent on the mould, pour 45% of the raw material mixture into the mold cavity, put the T-shaped steel skeleton, and then pour the remaining raw material mixture.
[0048] 3. Compression molding:
[0049] After all the raw material mixture is added to the mold cavity, close the mold, control the pressure at 200 tons, and control the temperature at 120°C. After keeping for 10 minutes, open the mold and eject it.
PUM
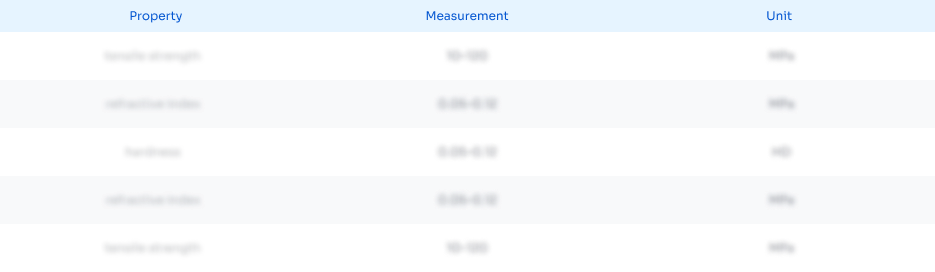
Abstract
Description
Claims
Application Information

- Generate Ideas
- Intellectual Property
- Life Sciences
- Materials
- Tech Scout
- Unparalleled Data Quality
- Higher Quality Content
- 60% Fewer Hallucinations
Browse by: Latest US Patents, China's latest patents, Technical Efficacy Thesaurus, Application Domain, Technology Topic, Popular Technical Reports.
© 2025 PatSnap. All rights reserved.Legal|Privacy policy|Modern Slavery Act Transparency Statement|Sitemap|About US| Contact US: help@patsnap.com