Process for preparing phosphine oxamate and its derivatives
A technology for glufosinate and derivatives is applied in the field of preparing glufosinate and derivatives thereof, which can solve the problems of increasing reaction by-products, difficult-to-separate impurities, increasing production costs and the like, and achieves saving production costs, high yield, high purity effect
- Summary
- Abstract
- Description
- Claims
- Application Information
AI Technical Summary
Problems solved by technology
Method used
Image
Examples
Embodiment 1
[0037] 5.61 g of freshly distilled acrolein (0.10 mol) were added to 6.00 g of acetic acid (0.10 mol) and added dropwise to 13.61 g of diethyl methylphosphonite (0.10 mol) at room temperature. After stirring for 2 h, it was added dropwise to 4.9 g of sodium cyanide (0.10 mol), 10.7 g of ammonium chloride (0.20 mol) in 50 ml of 25% ammonia solution, and the solution was brown. After stirring for 2h, it was added dropwise to 200ml of 37% hydrochloric acid without separation, and heated to reflux for 2h. Use a rotary evaporator at 50-60°C to basically evaporate the water to dryness to obtain a light yellow viscous substance. Add 125ml of methanol to dissolve, and filter to remove the solid ammonium chloride to obtain the filtrate. Methanol was distilled off, 15ml of distilled water was added, and the pH was adjusted to 3.0-3.5 with 5N sodium hydroxide solution. Add 40ml of methanol and place it at low temperature to precipitate 17.7g of white crystals. The product was analyzed...
Embodiment 2
[0039] 5.61 g of freshly distilled acrolein (0.10 mol) were added to 6.00 g of acetic acid (0.10 mol) and added dropwise to 13.61 g of diethyl methylphosphonite (0.10 mol) at room temperature. After stirring for 2 h, it was added dropwise to 4.9 g of sodium cyanide (0.10 mol), 10.7 g of ammonium chloride (0.20 mol) in 50 ml of 25% ammonia solution, and the solution was brown. After stirring for 2h, it was added dropwise to 200ml of 20% sodium hydroxide solution without separation, and heated to reflux for 2h. Use 5N sodium hydroxide solution to adjust the pH to 3.0-3.5, and then use a rotary evaporator at 50-60°C to basically evaporate the water to dryness to obtain a light yellow viscous substance. Add 125ml of methanol to dissolve, and filter to remove the solid sodium chloride to obtain the filtrate. Methanol was distilled off, 15ml of distilled water was added to dissolve, then 40ml of methanol was added, and placed at low temperature, 16.4g of white crystals were precipi...
Embodiment 3
[0041]5.61 g of freshly distilled acrolein (0.10 mol) was mixed with 6.00 g of acetic acid (0.10 mol) at room temperature to form a solution. This solution was added dropwise to a solution of 13.61 g of diethyl methylphosphonite (0.10 mol) and 4.6 g of ethanol (0.10 mol). After the mixture was stirred at room temperature for 2 h, it was added dropwise to 4.9 g of sodium cyanide (0.10 mol), 10.7 g of ammonium chloride (0.20 mol) in 50 ml of 25% ammonia solution, and the solution was brown. After stirring for 2 h, the crude aminonitrile was added dropwise to 200 ml of 37% hydrochloric acid. The mixture was heated to reflux for 3.5h. Use a rotary evaporator at 50-60°C to basically evaporate the water to dryness to obtain a light yellow viscous substance. Add 125ml of methanol to dissolve, and filter to remove the solid ammonium chloride to obtain the filtrate. Methanol was distilled off, 15ml of distilled water was added, and the pH was adjusted to 3.0-3.5 with 5N sodium hydro...
PUM
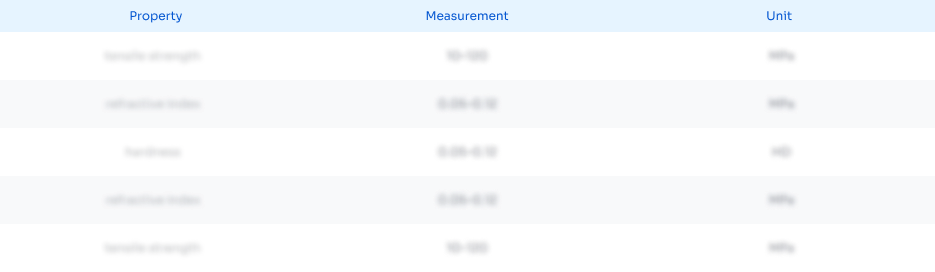
Abstract
Description
Claims
Application Information

- R&D
- Intellectual Property
- Life Sciences
- Materials
- Tech Scout
- Unparalleled Data Quality
- Higher Quality Content
- 60% Fewer Hallucinations
Browse by: Latest US Patents, China's latest patents, Technical Efficacy Thesaurus, Application Domain, Technology Topic, Popular Technical Reports.
© 2025 PatSnap. All rights reserved.Legal|Privacy policy|Modern Slavery Act Transparency Statement|Sitemap|About US| Contact US: help@patsnap.com