Optical printing head and its usage
A print head and optical technology, applied in the field of optical print heads, can solve the problems of shortening the service life of light emitting diodes 10a, reducing optical coupling efficiency, and high temperature
- Summary
- Abstract
- Description
- Claims
- Application Information
AI Technical Summary
Problems solved by technology
Method used
Image
Examples
Embodiment Construction
[0034] First, please refer to figure 2 , which is a schematic diagram of the system structure of the optical printer according to the present invention, including: a photosensitive drum unit 40, a power distribution unit 41, an optical print head unit 42, a developing unit 43, a transfer unit 44, paper 45, a heating unit 46 and Clear unit 47.
[0035] The photosensitive drum unit 40 is a core module in an optical printer, and has the characteristic of changing conductivity upon exposure to light. For example, after the exposure process, the photosensitive drum unit 40 has conductivity, and the unexposed part is an insulator.
[0036] The electricity distributing unit 41 is used for distributing electricity or eliminating static electricity on the surface of the photosensitive drum unit 40 , so as to generate a layer of static charge on the surface of the photosensitive drum unit 40 or eliminate the static electricity on the surface of the photosensitive drum unit 40 .
[003...
PUM
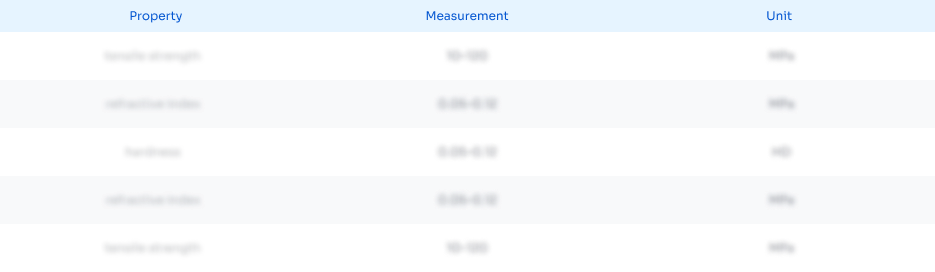
Abstract
Description
Claims
Application Information

- R&D
- Intellectual Property
- Life Sciences
- Materials
- Tech Scout
- Unparalleled Data Quality
- Higher Quality Content
- 60% Fewer Hallucinations
Browse by: Latest US Patents, China's latest patents, Technical Efficacy Thesaurus, Application Domain, Technology Topic, Popular Technical Reports.
© 2025 PatSnap. All rights reserved.Legal|Privacy policy|Modern Slavery Act Transparency Statement|Sitemap|About US| Contact US: help@patsnap.com