Submerged entry nozzle for continuous casting
An immersion and nozzle technology, applied in casting equipment, casting molten material containers, manufacturing tools, etc., can solve problems such as uneven flow rate and outflow rate, poor flow rate, and unevenness
- Summary
- Abstract
- Description
- Claims
- Application Information
AI Technical Summary
Problems solved by technology
Method used
Image
Examples
Embodiment Construction
[0055] To achieve the object of the invention, the invention proposes a submerged nozzle for continuous casting comprising: an inlet element made of refractory material and having a flared inlet; and other parts. Said other part comprises: an upper part, which continues from the inlet, and which has an elongated channel section with a large distance between the long sides and a small distance between the short sides as a whole and with a fixed cut-off area; a transition part (transit part), which continues from the upper part, the transition part has a nozzle wall and a slot-shaped flow channel section, the thickness of the nozzle wall gradually increases as the transition part extends farther towards the outlet of the nozzle Thinning, the distance between the short sides of the flow channel section gradually increases as the transition portion extends farther toward the outlet of the nozzle, and the distance between the long sides gradually increases as the transition portion ...
PUM
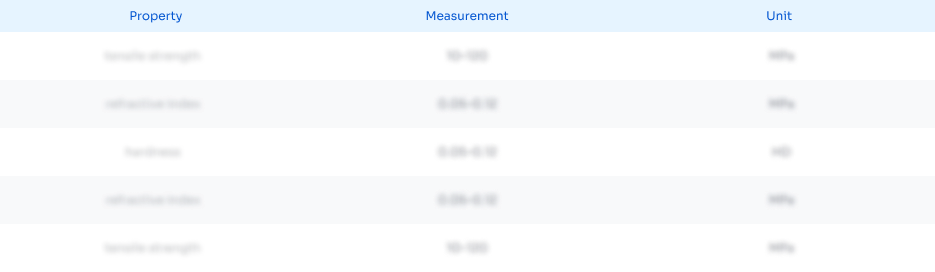
Abstract
Description
Claims
Application Information

- R&D
- Intellectual Property
- Life Sciences
- Materials
- Tech Scout
- Unparalleled Data Quality
- Higher Quality Content
- 60% Fewer Hallucinations
Browse by: Latest US Patents, China's latest patents, Technical Efficacy Thesaurus, Application Domain, Technology Topic, Popular Technical Reports.
© 2025 PatSnap. All rights reserved.Legal|Privacy policy|Modern Slavery Act Transparency Statement|Sitemap|About US| Contact US: help@patsnap.com