Synthesis reaction catalyst for loading type alkali metal biodiesel oil
A technology of biodiesel and synthesis reaction, applied in the direction of metal/metal oxide/metal hydroxide catalyst, physical/chemical process catalyst, catalyst activation/preparation, etc. The service life and other issues are solved, and the separation is simple and easy, the transesterification reaction is accelerated, and the operation cost and environmental cost are reduced.
- Summary
- Abstract
- Description
- Claims
- Application Information
AI Technical Summary
Problems solved by technology
Method used
Examples
Embodiment 1
[0012] Weigh LiNO 3 4.7467g, poured into a beaker, dissolved in 50ml deionized water, to get LiNO 3 solution. Weigh 9.55g CaO and pour it into the solution. After vigorously stirring for 2 h, place the beaker in an electric heating mantle to heat, and stir while evaporating until the solution is evaporated to dryness. Finally, it was dried overnight in an oven at 100°C. The dried powder aggregates are ground into powders less than 100 meshes to obtain the alkali metal supported transesterification catalyst Li / CaO.
[0013] In a 250ml flask, add 60ml of dried soybean oil, preheat to about 65°C in a water bath, add 15ml of methanol, catalyst Li / CaO 1.1076g (2% of oil weight), stir and reflux in a 65°C water bath. Keep the reflux reaction for 3.5 hours, and the reaction ends. Excess methanol is distilled off, and the reaction liquid phase is filtered while hot to separate the catalyst. The upper product is biodiesel, and the lower product is glycerol. The fatty acid methyl...
Embodiment 2
[0017] Weigh NaNO 3 6.0839g, poured into a beaker, dissolved in 100ml deionized water, to get NaNO 3 solution. Weigh 10.24g CaO and pour it into the solution. After vigorously stirring for 2 h, place the beaker in an electric heating mantle to heat, and stir while evaporating until the solution is evaporated to dryness. Finally, it was dried overnight in an oven at 100°C. Take out and grind into powder less than 100 mesh.
[0018] In a 250ml flask, add 60ml of dried soybean oil, preheat to about 65°C in a water bath, add 15ml of methanol, catalyst Na / CaO 1.1074g (2% of oil weight), stir and reflux in a 65°C water bath. After the reflux reaction was maintained for 3 hours, the reaction ended, excess methanol was distilled off, the reaction liquid phase was filtered while hot, and the catalyst was separated, and then the filtrate was poured into a separatory funnel and allowed to stand overnight for stratification. The upper product is biodiesel, and the lower product is g...
Embodiment 3
[0020] Weigh KNO 3 10.0922g, pour into a beaker, dissolve in 100ml deionized water, get KNO 3 solution. Weigh 10.24g CaO and pour it into the solution. After vigorously stirring for 2 h, place the beaker in an electric heating mantle to heat, and stir while evaporating until the solution is evaporated to dryness. Finally, it was dried overnight in an oven at 100°C. Take out and grind into powder less than 100 mesh.
[0021] In a 250ml flask, add 60ml of dried soybean oil, preheat to about 65°C in a water bath, add 15ml of methanol, catalyst K / CaO 1.1074g (2% of oil weight), stir and reflux in a 65°C water bath. Keep the reflux reaction for 4 hours and the reaction ends, distill off excess methanol, filter the reaction liquid phase while it is hot, separate the catalyst, and then pour the filtrate into a separatory funnel and let it stand overnight to separate layers. The upper product is biodiesel, and the lower product is glycerol. The content of fatty acid methyl este...
PUM
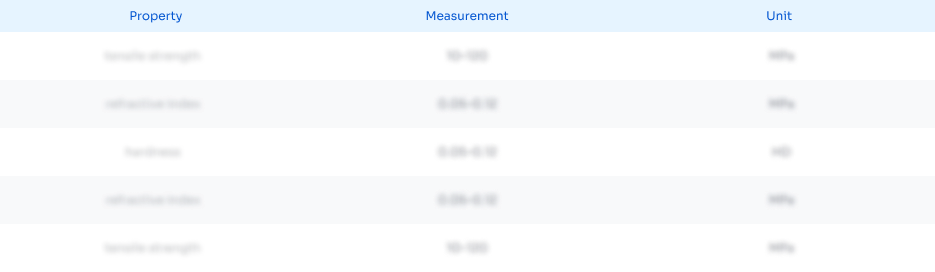
Abstract
Description
Claims
Application Information

- R&D Engineer
- R&D Manager
- IP Professional
- Industry Leading Data Capabilities
- Powerful AI technology
- Patent DNA Extraction
Browse by: Latest US Patents, China's latest patents, Technical Efficacy Thesaurus, Application Domain, Technology Topic, Popular Technical Reports.
© 2024 PatSnap. All rights reserved.Legal|Privacy policy|Modern Slavery Act Transparency Statement|Sitemap|About US| Contact US: help@patsnap.com