Variable capacitance micro electrostatic motor adopting five freedom degree static suspension
A variable capacitance and electrostatic suspension technology, applied in the direction of electrostatic generators/motors, generators/motors, electrical components, etc., can solve the problems of inductive coils that are not easy to miniaturize, inconvenient to adjust system characteristics, and low motor driving torque. Easy to process in large quantities, improve radial overload capacity, and improve the effect of rotor speed
- Summary
- Abstract
- Description
- Claims
- Application Information
AI Technical Summary
Problems solved by technology
Method used
Image
Examples
Embodiment Construction
[0019] The principle, structure and specific implementation of the present invention will be further described below in conjunction with the accompanying drawings.
[0020] figure 2 It is a schematic diagram of the overall structure of the micro electrostatic motor provided by the present invention. The electrostatic motor of the present invention adopts a sandwich structure (such as glass-silicon-glass), and the present invention is composed of a lower stator 1, an outer stator 2, a rotor 3, an inner stator 4, and an upper stator 5. The lower stator 1 is below the rotor, the upper stator 5 is above the rotor, the outer stator 2 is outside the rotor, and the inner stator 4 is inside the rotor. The lower stator 1, the outer stator 2, the inner stator 4 and the upper stator 5 form a closed The inner cavity, the rotor 3 is placed in the middle of this closed annular inner cavity, and the micron-level air gap 6 is maintained between the rotor 3 and the outer surface of the inner...
PUM
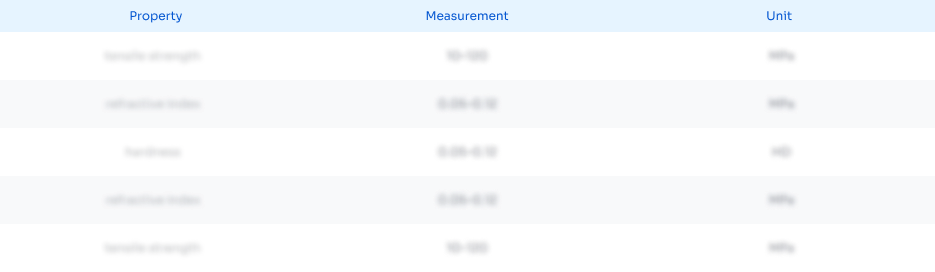
Abstract
Description
Claims
Application Information

- R&D
- Intellectual Property
- Life Sciences
- Materials
- Tech Scout
- Unparalleled Data Quality
- Higher Quality Content
- 60% Fewer Hallucinations
Browse by: Latest US Patents, China's latest patents, Technical Efficacy Thesaurus, Application Domain, Technology Topic, Popular Technical Reports.
© 2025 PatSnap. All rights reserved.Legal|Privacy policy|Modern Slavery Act Transparency Statement|Sitemap|About US| Contact US: help@patsnap.com