Mechanical cold method for making paper pulp
A technology of pulp and cold process, which is applied in the field of papermaking, can solve the problems of low pulp yield, serious environmental pollution, high production cost, etc., and achieve the effects of cost reduction, low environmental pollution and simple manufacturing method
- Summary
- Abstract
- Description
- Claims
- Application Information
AI Technical Summary
Problems solved by technology
Method used
Examples
Embodiment 1
[0010] Embodiment 1 of the present invention: use straw, wheat stalk, shuttleweed, bagasse, reed, awn stalk, cotton stalk or hemp stalk as papermaking raw materials separately, or use any two or Two or more or all of them are mixed in equal proportions or mixed together in any proportion as papermaking raw materials. The papermaking raw materials are chopped, then soaked in water, softened by steam, and processed into fiber velvet by a single spiral rubbing and separating machine. For raw materials, the single-spiral grinding and splitting machine is best to use the TMF type single-spiral grinding and splitting machine, and then the softened paper-making raw materials are ground by a high-concentration refiner with a model of ZDPHФ500-600 to obtain pulp. When the concentration of the obtained slurry is too high, an appropriate amount of water can be added, and the pulp can be obtained after the slurry is processed by a conventional screener. The pulp obtained in this embodimen...
Embodiment 2
[0011] Embodiment 2 of the present invention: use bamboo, wood, straw, wheat stalk, shuttleweed, bagasse, reed, awn stalk, cotton stalk or hemp stalk as papermaking raw materials separately, or use these several kinds of plants Any two or more than two kinds or all of them are mixed in equal proportions or mixed together in any proportion as papermaking raw materials. The papermaking raw materials are chopped, soaked in water, and processed into fiber velvet by TMFФ250 double-helix grinding and separating machine. After the raw materials are made, soften the velvet-like raw materials in the steaming ball or pulp tank, add 3-10% of the total weight of papermaking raw materials to the steaming ball or pulp tank, and inject 1-2 lbf / square inch pressure steam, keep it warm for 15-25 minutes, and then exhaust; then pass in steam with a pressure of 5-6 lbf / sqin, keep it at high pressure for 90-120 minutes, and then spray out the raw materials in the steaming ball or pulp tank togethe...
Embodiment 3
[0012] Embodiment 3 of the present invention: Bamboo or wood is mixed alone or in equal proportions, or mixed together in any proportion as paper-making raw materials, and the paper-making raw materials are chopped, soaked in water, and processed by a TMFФ250 double-helix grinding and separating machine. Fiber velvet-like raw materials, soften the fiber velvet-like raw materials by steam, and then grind the softened raw materials through a high-concentration refiner to obtain a slurry. After the slurry is processed by a refiner and a screener, it can be Pulp is obtained for making fine paper on a conventional paper machine. The pulp obtained in this embodiment can be used to make cultural papers such as typing paper, writing paper, and newsprint by conventional paper machines.
PUM
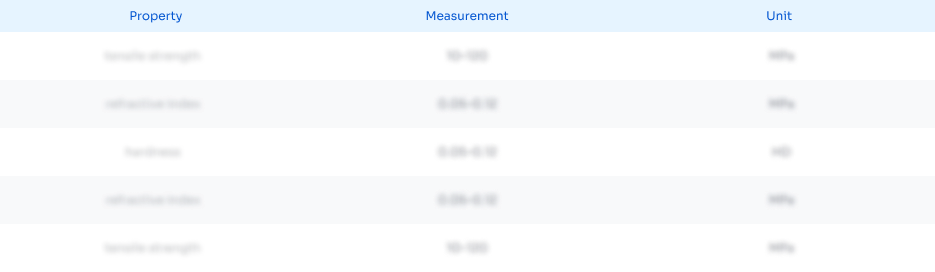
Abstract
Description
Claims
Application Information

- R&D
- Intellectual Property
- Life Sciences
- Materials
- Tech Scout
- Unparalleled Data Quality
- Higher Quality Content
- 60% Fewer Hallucinations
Browse by: Latest US Patents, China's latest patents, Technical Efficacy Thesaurus, Application Domain, Technology Topic, Popular Technical Reports.
© 2025 PatSnap. All rights reserved.Legal|Privacy policy|Modern Slavery Act Transparency Statement|Sitemap|About US| Contact US: help@patsnap.com