Permanent magnet motor rotor capable of automatic weaking magnet following rotation speed
A permanent magnet motor and automatic technology, applied in the direction of magnetic circuit rotating parts, magnetic circuit shape/style/structure, etc., can solve the problems of large rotor flux leakage, system efficiency drop, low torque, etc., to reduce magnetic flux leakage , Improve utilization efficiency, improve the effect of torque
- Summary
- Abstract
- Description
- Claims
- Application Information
AI Technical Summary
Problems solved by technology
Method used
Image
Examples
specific Embodiment approach 1
[0006] Specific implementation mode one: the following combination figure 1 This embodiment will be specifically described. It consists of a rotor core 1, several main pole permanent magnets 3, and several auxiliary permanent magnets 4. The rotor core 1 is cylindrical, and there is a shaft hole 6 for assembling the rotating shaft at the center of the rotor core 1. Several radial chutes 9 are distributed, and each radial chute 9 is inlaid with a main pole permanent magnet 3 and the main pole permanent magnet 3 is shorter than the length of the radial chute 9, and the outer surface of the radial chute 9 An auxiliary permanent magnet 4 is fixed at the end, and both the main pole permanent magnet 3 and the auxiliary permanent magnet 4 are tangentially magnetized and the magnetization direction of the main pole permanent magnet 3 and the auxiliary permanent magnet 4 in the same radial chute 9 is the same , the adjacent side surfaces of the two adjacent main pole permanent magnets...
specific Embodiment approach 2
[0007] Specific implementation mode two: the following combination figure 1 This embodiment will be specifically described. There is a magnetic isolation groove 2 on both sides of the radial chute 9, two magnetic isolation grooves 2 take the radial chute 9 as the symmetrical center, and the magnetic isolation groove 2 is opened at the outer end of the radial chute 9 . Other components and connections are the same as those in Embodiment 1. In this embodiment, "the reluctance of the rotor core 1 at the inner end of the radial chute 9 is smaller than the reluctance of the rotor core 1 at the outer end of the radial chute 9" is realized by separating the magnetic slot 2, the structure is simple, and the process is easy to realize . The function of the magnetic isolation groove 2 is to reduce the magnetic flux sent by the main pole permanent magnet 3 when the main pole permanent magnet 3 moves outwards into its position, so its size and shape are not unique, and can be rectangu...
specific Embodiment approach 3
[0008] Specific implementation mode three: the following combination figure 2 This embodiment will be specifically described. The difference between this embodiment and the second embodiment is that it also includes a non-magnetically conductive plate 8 , which is arranged on both sides of the radial chute 9 and located at the outer end of the radial chute 9 . In this embodiment, "the reluctance of the rotor core 1 at the inner end of the radial chute 9 is smaller than the reluctance of the rotor core 1 at the outer end of the radial chute 9" is realized by setting the non-magnetic conductive plate 8, and the two non-magnetic conductive plates 8 is also equivalent to the auxiliary slideway of the main pole permanent magnet 3, so that the main pole permanent magnet 3 can slide smoothly in the radial slide groove 9. Other compositions and connections are the same as those in Embodiment 2.
PUM
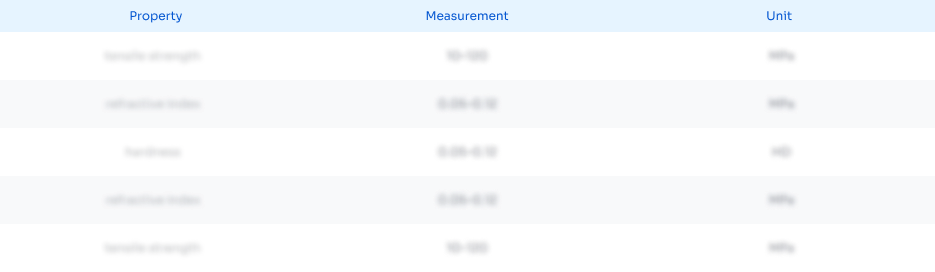
Abstract
Description
Claims
Application Information

- R&D Engineer
- R&D Manager
- IP Professional
- Industry Leading Data Capabilities
- Powerful AI technology
- Patent DNA Extraction
Browse by: Latest US Patents, China's latest patents, Technical Efficacy Thesaurus, Application Domain, Technology Topic, Popular Technical Reports.
© 2024 PatSnap. All rights reserved.Legal|Privacy policy|Modern Slavery Act Transparency Statement|Sitemap|About US| Contact US: help@patsnap.com