Surface processing and forming method of photoresist layer
A technology of photoresist layer and photoresist, which is applied in the direction of photosensitive material processing, electrical components, semiconductor/solid-state device manufacturing, etc., can solve the problems of film layer pattern distortion, contour distortion, and resolution reduction, etc. achieve the effect of avoiding deformation
- Summary
- Abstract
- Description
- Claims
- Application Information
AI Technical Summary
Problems solved by technology
Method used
Image
Examples
Embodiment Construction
[0031] Since the patterned photoresist layer obtained by the photolithography process tends to be deformed or collapsed when the line width becomes larger and larger, the present invention proposes a surface of the photoresist layer approach to deal with the above problems. The surface treatment method of this photoresist layer is to use photolithographic equipment to form a patterned photoresist layer on the wafer, and then move the wafer to the etching reaction, using at least hydrogen bromide or iodine A reaction gas of hydrogen hydride is used to perform a surface treatment step on the photoresist layer to form a hardened layer on the surface of the photoresist layer.
[0032] The above surface treatment step uses radio frequency voltage to excite the reactive gas into plasma to form a hardened layer on the surface of the photoresist layer, and the hardened layer can effectively maintain the profile of the patterned photoresist layer. In addition, the material of the abov...
PUM
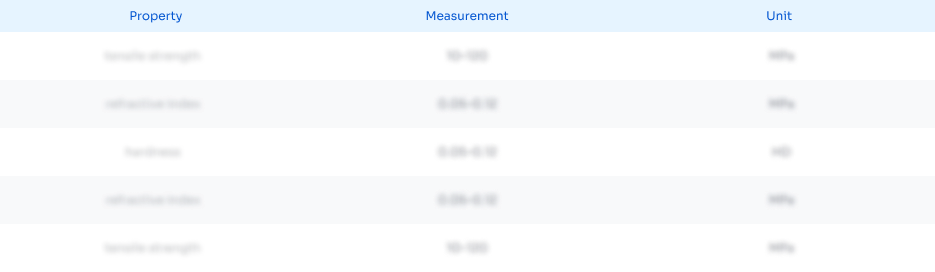
Abstract
Description
Claims
Application Information

- R&D
- Intellectual Property
- Life Sciences
- Materials
- Tech Scout
- Unparalleled Data Quality
- Higher Quality Content
- 60% Fewer Hallucinations
Browse by: Latest US Patents, China's latest patents, Technical Efficacy Thesaurus, Application Domain, Technology Topic, Popular Technical Reports.
© 2025 PatSnap. All rights reserved.Legal|Privacy policy|Modern Slavery Act Transparency Statement|Sitemap|About US| Contact US: help@patsnap.com