Magnetically controlled sputtering process
A manufacturing process and magnetron sputtering technology, applied in the field of thin film deposition manufacturing process, can solve the problems of fracture or buried hole 16, the influence of coating yield is greatly affected, and achieve the effect of improving coating yield
- Summary
- Abstract
- Description
- Claims
- Application Information
AI Technical Summary
Problems solved by technology
Method used
Image
Examples
Embodiment Construction
[0015] Figure 3A It is a schematic diagram of a reaction chamber used in a magnetron sputtering manufacturing process of a preferred embodiment of the present invention. Please refer to Figure 3A , The magnetron sputtering manufacturing process of this embodiment includes the following steps. Firstly, a reaction chamber 200 (reaction chamber) is firstly provided. The reaction chamber 200 at least includes a substrate base 110, a target 210, a magnetron device 130, and a process gas 140. The material of the target 210 is, for example, aluminum or an aluminum alloy. Or it is a metal whose melting point is higher than that of aluminum or aluminum alloy, such as metals such as chromium, molybdenum, tungsten, titanium or tantalum or alloys thereof. The substrate holder 110 can fix the substrate 10 in the reaction chamber 200 and can heat the substrate 10 .
[0016] Please continue to refer to Figure 3A , the substrate holder 110 and the target material 210 are arranged in th...
PUM
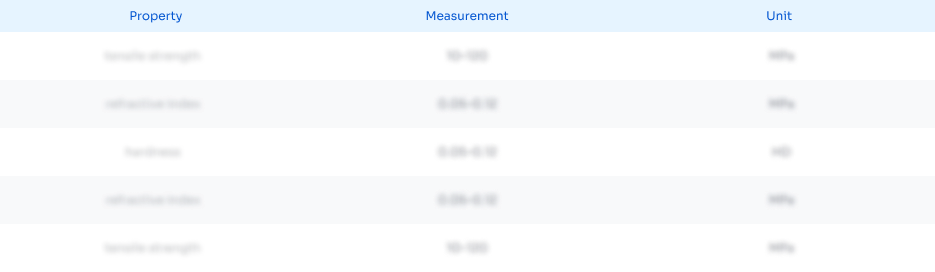
Abstract
Description
Claims
Application Information

- R&D Engineer
- R&D Manager
- IP Professional
- Industry Leading Data Capabilities
- Powerful AI technology
- Patent DNA Extraction
Browse by: Latest US Patents, China's latest patents, Technical Efficacy Thesaurus, Application Domain, Technology Topic, Popular Technical Reports.
© 2024 PatSnap. All rights reserved.Legal|Privacy policy|Modern Slavery Act Transparency Statement|Sitemap|About US| Contact US: help@patsnap.com