Process for preparing antibacterial polyacrylonitrile fiber
A technology of polyacrylonitrile fiber and acrylonitrile, applied in the direction of wet spinning, etc., can solve the problem of no bactericidal performance, and achieve the effect of strong antibacterial ability, long-lasting antibacterial performance and broad application prospects
- Summary
- Abstract
- Description
- Claims
- Application Information
AI Technical Summary
Problems solved by technology
Method used
Image
Examples
example 1
[0027] In a 3-liter reactor equipped with mechanical stirring and temperature controller, add 0.784 kg of water and 0.816 kg of sodium thiocyanate in a certain proportion. After the dissolution is complete, add 315 g of acrylonitrile and 25 g of 3-allyl 5,5-dimethylcaprolactoin, 1.02 grams of isopropanol and 1.75 grams of azobisisobutyronitrile. After stirring evenly, the temperature was raised to 78° C. for 2 hours to react. Cool after the reaction, and remove unreacted acrylonitrile under reduced pressure. The measured solid content of the solution was 12.4%, and the mass percentage of the 3-allyl-5,5-dimethylcaprolactone component in the copolymer was 1.6%. After the obtained solution was left to defoam under vacuum and filtered, the spinning solution was obtained. The spinning solution is pressed into the coagulation bath through the spinneret, the coagulation bath is 10% sodium thiocyanate aqueous solution, and the temperature is 10°C. The spun silk pulling speed was 2...
example 2
[0030] In a 3-liter reactor equipped with mechanical stirring and temperature controller, 1.2 kilograms of water, 120 grams of acrylonitrile, 54.3 grams of 3-allyl-5,5-dimethylcaprolactin were added in a certain proportion, Then 2.45 grams of potassium persulfate was added. After stirring evenly, the temperature was raised to 72° C. to react for 2 hours. After the reaction, cool, filter and wash with water. The resulting white powder of the copolymer was vacuum-dried at 80 °C to constant weight. Get 0.10 kilogram of copolymer powder, 0.90 kilogram of industrial spinning grade polyacrylonitrile copolymer (91.2% of acrylonitrile content, 7.8% of methyl acrylate, 1.0% of sodium methacrylic sulfonate) 0.90 kilogram, after stirring, dissolve together in 7.33 kilogram In 51% sodium thiocyanate aqueous solution, the dissolution time is 6 hours and the temperature is 60°C. A solution with a solid content of 12.0% was obtained, and after defoaming and filtering, a spinning solution ...
example 3
[0033]Get 0.20 kg of copolymer powder prepared in Example 2, 0.80 kg of industrial spinning grade polyacrylonitrile copolymer (acrylonitrile content 91.2%, methyl acrylate 7.8%, sodium methacrylate sulfonate 1.0%), stir , were dissolved together in 7.33 kg of 51% sodium thiocyanate aqueous solution, the dissolution time was 6 hours, and the dissolution temperature was 60°C. The obtained solution has a solid content of 12.0%, and after defoaming and filtering, a spinning solution is obtained. The spinning solution is pressed into the coagulation bath through the spinneret, the coagulation bath is 10% sodium thiocyanate aqueous solution, and the temperature is 10°C. The spun silk pulling speed was 2.5 m / min. The as-spun fibers were preheated in water at 55°C and stretched 1.5 times. Then wash with desalted water at 50°C, and then heat-stretch in water at a temperature of 96-99.5°C, and the stretching ratio is 6 times. The total draw ratio of the fiber is 9 times. After the s...
PUM
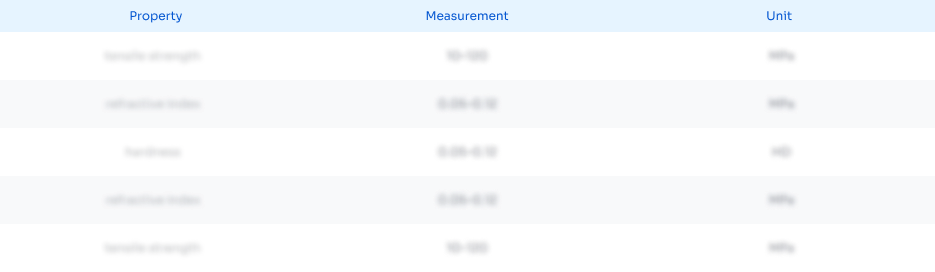
Abstract
Description
Claims
Application Information

- R&D Engineer
- R&D Manager
- IP Professional
- Industry Leading Data Capabilities
- Powerful AI technology
- Patent DNA Extraction
Browse by: Latest US Patents, China's latest patents, Technical Efficacy Thesaurus, Application Domain, Technology Topic, Popular Technical Reports.
© 2024 PatSnap. All rights reserved.Legal|Privacy policy|Modern Slavery Act Transparency Statement|Sitemap|About US| Contact US: help@patsnap.com