High speed on line electrolysis sharpening grinding liquid suitable for bronze binding agent ultra hard abrasive
A technology of superabrasives and bonding agents, applied in the field of grinding fluid, can solve the problems of difficult manufacturing of grinding wheels, less application, and influence on the popularization and application of grinding wheels and grinding fluids, and achieve good compactness, rapid drop in electrolysis current, and good electrolysis The effect of film-forming ability
- Summary
- Abstract
- Description
- Claims
- Application Information
AI Technical Summary
Problems solved by technology
Method used
Image
Examples
Embodiment 1
[0029] Embodiment 1: get base fluid (No. 420 grinding fluid) 87.77%, sodium nitrite 11%, sodium nitrate 0.25%, disodium hydrogen phosphate 0.5%, sodium tetraborate 0.1%, glycerol 0.28% by mass percentage, Tributyl phosphate 0.1%, first put the required quality of insoluble disodium hydrogen phosphate into a certain quality of hot water or warm water, and stir it continuously with a glass rod to fully dissolve it; secondly, dilute the base liquid with water according to the usage Requirements and required mass dilution (the quality of added water should take into account the quality of water used to dissolve disodium hydrogen phosphate before); again, add the disodium hydrogen phosphate solution that has just been dissolved into the base liquid, and keep stirring to make Mix it evenly; then, add easily soluble sodium nitrite, sodium nitrate, sodium tetraborate, tributyl glycerol phosphate into the base liquid one by one according to the required mass ratio, and stir continuously...
Embodiment 2
[0030] Embodiment 2: Get base fluid (No. 420 grinding fluid) 87.78%, sodium nitrite 9%, sodium nitrate 0.40%, disodium hydrogen phosphate 2.0%, sodium tetraborate 0.2%, glycerol 0.32% by mass percentage, Tributyl phosphate 0.3%, first, put the required quality of insoluble disodium hydrogen phosphate into a certain quality of hot water or warm water, and stir it with a glass rod to make it fully dissolved; secondly, dilute the base liquid with water according to the Use requirements and required quality dilution (the quality of added water will take into account the quality of water used to dissolve disodium hydrogen phosphate before); again, add the disodium hydrogen phosphate solution that has just been dissolved into the base liquid, and keep stirring, Make it evenly mixed; then, add easily soluble sodium nitrite, sodium nitrate, sodium tetraborate, tributyl glycerol phosphate into the base liquid one by one according to the required mass ratio, and keep stirring to make it ...
Embodiment 3
[0031]Embodiment 3: Get base fluid (No. 420 grinding fluid) 88.78%, sodium nitrite 9%, sodium nitrate 0.32%, disodium hydrogen phosphate 1.25%, sodium tetraborate 0.15%, glycerol 0.3% by mass percentage, Tributyl phosphate 0.2%, first, put the required quality of insoluble disodium hydrogen phosphate into a certain quality of hot water or warm water, and stir it with a glass rod to make it fully dissolved; secondly, dilute the base liquid with water according to the Use requirements and required quality dilution (the quality of added water will take into account the quality of water used to dissolve disodium hydrogen phosphate before); again, add the disodium hydrogen phosphate solution that has just been dissolved into the base liquid, and keep stirring, Make it evenly mixed; then, add easily soluble sodium nitrite, sodium nitrate, sodium tetraborate, tributyl glycerol phosphate into the base liquid one by one according to the required mass ratio, and keep stirring to make it ...
PUM
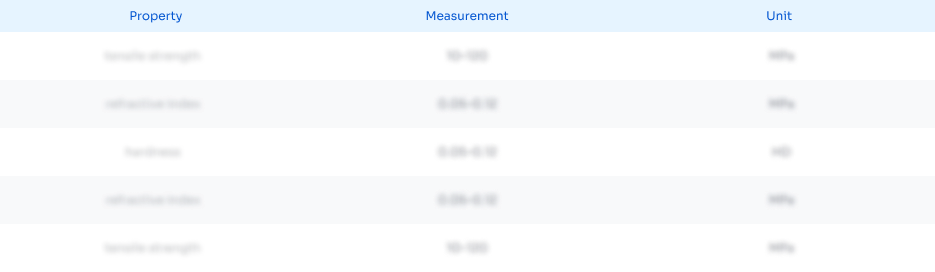
Abstract
Description
Claims
Application Information

- R&D
- Intellectual Property
- Life Sciences
- Materials
- Tech Scout
- Unparalleled Data Quality
- Higher Quality Content
- 60% Fewer Hallucinations
Browse by: Latest US Patents, China's latest patents, Technical Efficacy Thesaurus, Application Domain, Technology Topic, Popular Technical Reports.
© 2025 PatSnap. All rights reserved.Legal|Privacy policy|Modern Slavery Act Transparency Statement|Sitemap|About US| Contact US: help@patsnap.com