Forming electromagnetic communication circuit components using densified metal powder
A metal powder and integrated circuit technology, applied in the direction of circuits, printed circuits, electrical components, etc., can solve the problems of reducing the total conductivity of circuit patterns, weak conductors of circuits, etc., and achieve the minimum process cost and pollution, easy recycling, and low cost Effect
- Summary
- Abstract
- Description
- Claims
- Application Information
AI Technical Summary
Problems solved by technology
Method used
Image
Examples
Embodiment 1
[0083] This example illustrates the calculation of a sample figure of merit (FOM). Using %FOM, for pure copper, the measured resistance of the pressed powder pattern compared to the smallest possible theoretical resistivity satisfies the following equation:
[0084] %FOM=(R theoretical / R measured )×100
[0085] where R theoretical is the resistivity of pure copper, and R is calculated from the measured resistance of the sample pressed powder pattern measured .
[0086] The density of solid copper is 8.96g / cm 3 . The resistivity of copper is 1.73×10 -6 Ohm-centimeter (ohms-cm). For the mass and profile of the sample, for normalization, the mass (grams) per unit length (cm) and the resistance (ohms) per unit length (cm) are plugged into the FOM equation such that:
[0087] %FOM=(R theoretical / R measured )×100
[0088] where: R theoretieal =(Copper Density)(Copper Resistivity)=0.0000155g-ohm / cm 2
[0089] R measured =[(mass in grams per centimeter)(per centimete...
Embodiment 2
[0094] Copper powder (dendritic, 3 microns, 99.7%) from Sigma-Aldrich (Milwaukee WI) was cleaned by stirring it in a solution of hydrochloric acid containing 10% water, followed by 1 water rinse and 3 ethanol rinses. The copper powder can be air dried for approximately 1 hour. A 20 cm diameter #270 molecular sieve was placed over a 20 cm diameter, 46 cm long cardboard tube. Cardboard tubes were placed over seven sets of 55 cm diameter model 54 Whatman filter paper circles. Tin powder (AEE 1-5 micron 99.9%), then copper powder was sprayed on molecular sieves and allowed to settle on the filter paper to a depth varying from about 0.1 mm to 0.5 mm for each sample. In the following examples, this method of applying one or more metal powders to a substrate is referred to as a sieving method.
[0095] In a first step, the patterned mold was pressed onto the powder by applying 27 megapascals (MPa) on the powder and filter paper using a Carver platen press (Model 3891, Wabash, India...
Embodiment 3-8
[0099] Examples 3-8 were prepared using the sieving method of Example 2. In one step, metal powder was captured into a pattern and densified by pressing a patterned die onto the powder at the pressures shown in Table 1. As shown in Table 1, two different paperboards and combinations of metal powder and particle types were used. The resistance of each sample was measured and Table 1 shows the calculated %FOM.
[0100] Table 1 shows the results using combinations of substrates and metal powders under different condition sets. Table 2 shows abbreviations for substrates and metals.
PUM
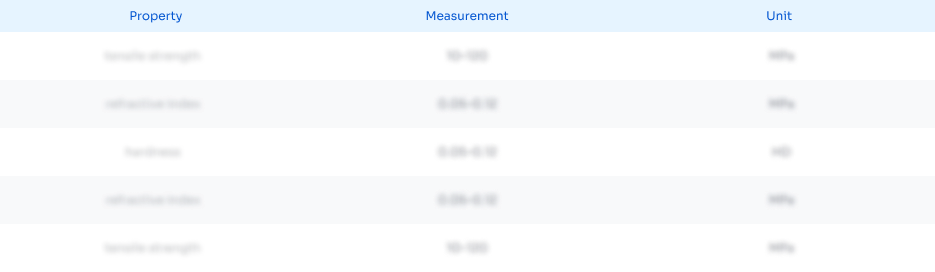
Abstract
Description
Claims
Application Information

- R&D Engineer
- R&D Manager
- IP Professional
- Industry Leading Data Capabilities
- Powerful AI technology
- Patent DNA Extraction
Browse by: Latest US Patents, China's latest patents, Technical Efficacy Thesaurus, Application Domain, Technology Topic, Popular Technical Reports.
© 2024 PatSnap. All rights reserved.Legal|Privacy policy|Modern Slavery Act Transparency Statement|Sitemap|About US| Contact US: help@patsnap.com