Linseed oil modified phenol formaldehyde resin for friction material and its preparation method
A technology of linseed oil modification and phenolic resin, which is applied in the field of friction composite materials, can solve the problems of difficult stability of modified phenolic resin, poor high-temperature performance of phenolic resin, cumbersome purification process, etc., and achieve performance and environmental benefits. Excellent heat resistance and friction and wear performance, easy purification effect
- Summary
- Abstract
- Description
- Claims
- Application Information
AI Technical Summary
Problems solved by technology
Method used
Examples
Embodiment 1
[0028] Add 100g of phenol and 0.15g of p-toluenesulfonic acid into the reaction kettle, slowly add 45g of linseed oil under rapid stirring, raise the temperature to 135°C, and react for 2 hours, stop heating and cool to room temperature under stirring to obtain the linseed oil-phenol reaction Under the condition of heating and stirring, add 126g of formaldehyde, stir well and add 4.5g of ammonia water, slowly raise the temperature to 115°C, when the reactant appears yellow and turbid, cool it, and start vacuum dehydration until 50°C, when the resin liquid turns brown When transparent, stop dehydration, add absolute ethanol and stir to dissolve, cool to room temperature and discharge to obtain 248g linseed oil modified phenolic resin.
Embodiment 2
[0030] Add 100g of phenol and 0.17g of p-toluenesulfonic acid into the reaction kettle, slowly add 50g of linseed oil under rapid stirring, raise the temperature to 140°C, and after 3 hours of reaction, stop heating and cool to room temperature under stirring to obtain the linseed oil-phenol reaction Under the condition of heating and stirring, add 130g of formaldehyde, add 6g of ammonia water after stirring evenly, slowly raise the temperature to 105°C, when the reactant appears yellow and turbid, cool it down, and start vacuum dehydration until 50°C, when the resin liquid turns brown and transparent , stop dehydration, add absolute ethanol and stir to dissolve, cool to room temperature and discharge to obtain 256g linseed oil modified phenolic resin.
Embodiment 3
[0032] Add 100g of phenol and 0.20g of p-toluenesulfonic acid into the reaction kettle, slowly add 55g of linseed oil under rapid stirring, raise the temperature to 145°C, and react for 4 hours, stop heating and cool to room temperature under stirring to obtain the linseed oil-phenol reaction Under the condition of heating and stirring, add 135g of formaldehyde, stir well and add 7.5g of ammonia water, slowly raise the temperature to 110°C, when the reactant appears yellow and turbid, cool it, and start vacuum dehydration until 50°C, when the resin liquid turns brown When it is transparent, stop dehydration, add absolute ethanol and stir to dissolve, cool to room temperature and discharge to obtain 252 g of linseed oil modified phenolic resin.
PUM
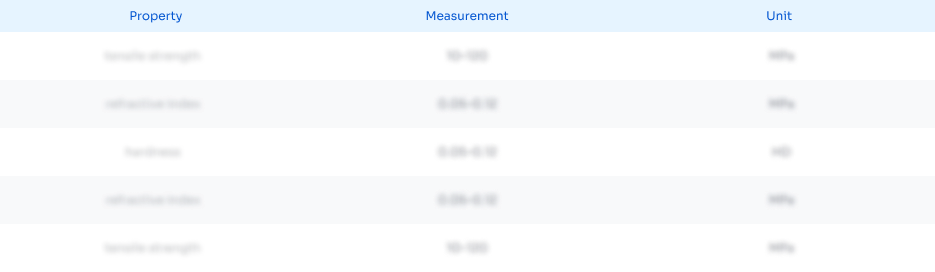
Abstract
Description
Claims
Application Information

- Generate Ideas
- Intellectual Property
- Life Sciences
- Materials
- Tech Scout
- Unparalleled Data Quality
- Higher Quality Content
- 60% Fewer Hallucinations
Browse by: Latest US Patents, China's latest patents, Technical Efficacy Thesaurus, Application Domain, Technology Topic, Popular Technical Reports.
© 2025 PatSnap. All rights reserved.Legal|Privacy policy|Modern Slavery Act Transparency Statement|Sitemap|About US| Contact US: help@patsnap.com