Antigravity vacuum sucking cast process for preparing aluminium base composite material
An aluminum-based composite material, vacuum suction casting technology, applied in the field of casting, can solve the problem of unable to form aluminum-based composite materials, etc., to achieve the effect of improving mechanical properties
- Summary
- Abstract
- Description
- Claims
- Application Information
AI Technical Summary
Problems solved by technology
Method used
Examples
Embodiment 1
[0021] 5wt.%TiB 2p / ZL109 composite material melts at 680 ° C, through N 2 protection, stir for 15 minutes after melting, close the middle partition, turn off the N 2 , the lower chamber is vacuumed and refined, and the refining time is 5 minutes. After the vacuum refining is completed, the lower chamber is connected to N 2 , to protect the refined melt, install the liquid riser, the cavity and the sleeve, after the installation, the upper cavity is vacuumed, and the vacuum degree of the upper cavity reaches -0.03MPa within 5s, and the vacuum is maintained for 1s, and the lower cavity is connected to N 2 , the lower cavity pressure reaches 0.1MPa, after 1min, turn off the vacuum, turn off the N 2 , the filling is completed, the sleeve and the cavity are removed, and the parts are taken out. T5 state mechanical properties of prepared materials: σ b =355Mpa; σ 0.2 =323Mpa; δ=3.5%; E=82.1Gpa.
Embodiment 2
[0023] 12wt.%TiC p / ZL101 composite material melts at 750 ° C, through Ar 2 protection, stir for 50 minutes after melting, close the middle partition, and close the Ar 2 , the lower chamber is vacuumed and refined, and the refining time is 40 minutes. After the vacuum refining is completed, the lower chamber is connected to Ar 2 , to protect the refined melt, install the liquid riser, cavity and sleeve, after the installation is completed, the upper cavity is vacuumed, and the vacuum degree of the upper cavity reaches -0.1MPa within 20s, and the vacuum is maintained for 10s, and the lower cavity is connected to Ar 2 , the lower cavity pressure reaches 0.5MPa, after 5min, turn off the vacuum, turn off the Ar 2 , the filling is completed, the sleeve and the cavity are removed, and the parts are taken out. T6 state mechanical properties of prepared materials: σ b =435Mpa; σ 0.2 = 417Mpa; δ = 1.2%; E = 86.7Gpa.
Embodiment 3
[0025] Will (4wt.%TiB 2 +4wt.%TiC) / ZL114 composite melted at 720°C, passed N 2 protection, stir for 30 minutes after melting, close the middle partition, turn off the N 2 , the lower chamber is vacuumed and refined, and the refining time is 20 minutes. After the vacuum refining is completed, the lower chamber is connected to N 2 , to protect the refined melt, install the liquid riser, cavity and sleeve, after the installation is completed, the upper cavity is vacuumed, and the vacuum degree of the upper cavity reaches -0.07MPa within 10s, and the vacuum is maintained for 5s, and the lower cavity is connected to N 2 , the lower chamber pressure reaches 0.3MPa, after 3min, turn off the vacuum, turn off the N 2 , the filling is completed, the sleeve and the cavity are removed, and the parts are taken out. T6 state mechanical properties of prepared materials: σ b =383Mpa; σ 0.2 =353Mpa; δ=3.3%; E=83.8Gpa.
PUM
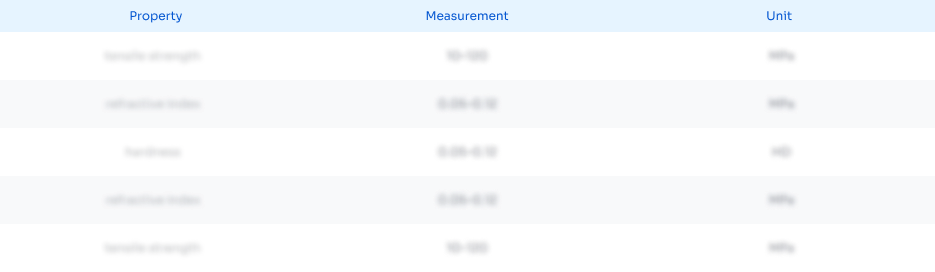
Abstract
Description
Claims
Application Information

- Generate Ideas
- Intellectual Property
- Life Sciences
- Materials
- Tech Scout
- Unparalleled Data Quality
- Higher Quality Content
- 60% Fewer Hallucinations
Browse by: Latest US Patents, China's latest patents, Technical Efficacy Thesaurus, Application Domain, Technology Topic, Popular Technical Reports.
© 2025 PatSnap. All rights reserved.Legal|Privacy policy|Modern Slavery Act Transparency Statement|Sitemap|About US| Contact US: help@patsnap.com