Image pickup device and camera module
A technology of image pickup device and wiring diagram, which is applied in the direction of camera, camera body, image communication, etc., and can solve problems such as bad signal, signal becoming noise, and image quality degradation
- Summary
- Abstract
- Description
- Claims
- Application Information
AI Technical Summary
Problems solved by technology
Method used
Image
Examples
no. 1 approach
[0069] 1A is a plan view showing an example structure of an image pickup device according to a first embodiment of the present invention. FIG. 1B is a side view viewed from the left side of FIG. 1A . Fig. 1C is a side view as viewed from the bottom side of Fig. 1A. FIG. 1D is a bottom view of FIG. 1A.
[0070] As shown in FIGS. 1A to 1D , the image pickup device 20 is constituted by a CCD image sensor or a CMOS image sensor or the like that converts incident light from the outside (light from an object) into an electric signal. A light receiving unit 22 for light from an object is provided in a central portion of the surface of an image pickup device main body unit (device main body unit) 21 . The light receiving unit 22 is included in an image pickup unit that forms an image of an object by converting incident light into an electrical signal (optical signal). Electrodes 23 (bonding sheets) are provided around the light receiving unit 22 . Protruding electrodes 24 (solderi...
no. 2 approach
[0090] In the first embodiment, the light-transmitting conductive layer 26 is provided in the signal wiring portion (the electrode 23 : A to D, F and G and the wiring pattern 25 connected thereto and the portion of the conductive unit of the power supply wiring portion has one or more openings in it. However, in the second embodiment, the surface of the image pickup device main body unit 21 is covered with the light-transmitting insulating layer 27 which will be described later at the portion corresponding to the ground wiring (electrodes 23: E and H and There are one or more openings in the portion of the conductive unit connected thereto to the wiring pattern 25 ), and furthermore, a light-transmitting conductive layer 26A to be described later is provided over the light-transmitting insulating layer 27 .
[0091] 5A is a plan view of a second embodiment of the image pickup device of the present invention. Fig. 5B is a side view viewed from the left side of Fig. 5A. Fig. 5...
no. 3 approach
[0110] In the first and second embodiments, the front side of the image pickup device main body unit 21 (or 21A) is covered with the light-transmitting conductive layer 26 or 26A, and thus its inside is magnetically shielded. In the third embodiment, similarly to the case of having the light-transmitting conductive layer 26 or 26A, the back side (which may also include side surfaces) is also additionally covered with the light-transmitting conductive layer.
[0111] In the case of the back surface of the image pickup device main body unit 21, similarly to the case where the light-transmitting conductive layer 26 is provided on the front surface, the light-transmissive conductive layer is formed in a position corresponding to the protrusion provided on the back surface side of the image pickup device main body unit 21. The electrode 24 (soldering bump) and the wiring pattern 25 connected thereto, the signal wiring portion (bump electrodes 24; A to D, F and G and the wiring patte...
PUM
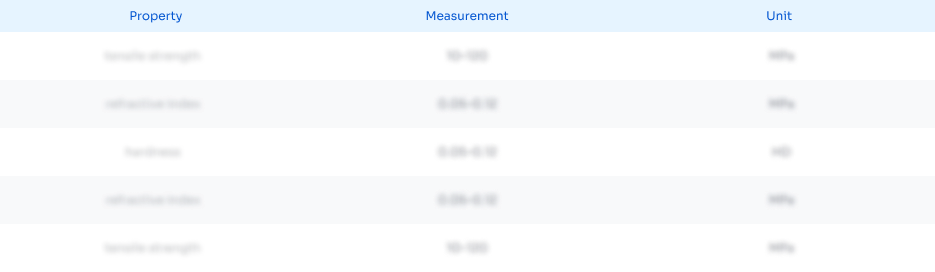
Abstract
Description
Claims
Application Information

- R&D
- Intellectual Property
- Life Sciences
- Materials
- Tech Scout
- Unparalleled Data Quality
- Higher Quality Content
- 60% Fewer Hallucinations
Browse by: Latest US Patents, China's latest patents, Technical Efficacy Thesaurus, Application Domain, Technology Topic, Popular Technical Reports.
© 2025 PatSnap. All rights reserved.Legal|Privacy policy|Modern Slavery Act Transparency Statement|Sitemap|About US| Contact US: help@patsnap.com