Method for manufacturing rustproof coated steel strand
A manufacturing method and technology for steel strands, which are applied in textiles, papermaking, auxiliary devices for rope making, coatings, etc. The effect of reducing transportation costs, eliminating heating devices, and reducing processes
- Summary
- Abstract
- Description
- Claims
- Application Information
AI Technical Summary
Problems solved by technology
Method used
Image
Examples
Embodiment Construction
[0036] figure 1 It is a schematic diagram of the manufacturing apparatus of the antirust coated steel strand used in the method of this invention.
[0037] This rust-proof coated steel strand manufacturing device includes: a stranding machine 2 for stranding a plurality of steel core wires 1 and 1 into a strand A; 3. A cross-head type synthetic resin extrusion molding machine for filling the space between the steel core wires 1, 1.. of the steel strand A with thermoplastic synthetic resin material. 4. Coating the synthetic resin material on the steel strand The cross-head type synthetic resin extrusion molding machine 5 and the cooling device 6 on the outer periphery of the strand A manufacture the rust-proof coated steel strand B by sequentially completing the stranding process, the bluing process, the rust-proof coating process, and the cooling process .
[0038] The stranding machine 2 has: a wire reel 7, 7.. for winding each steel core wire 1, 1, and each steel core wire...
PUM
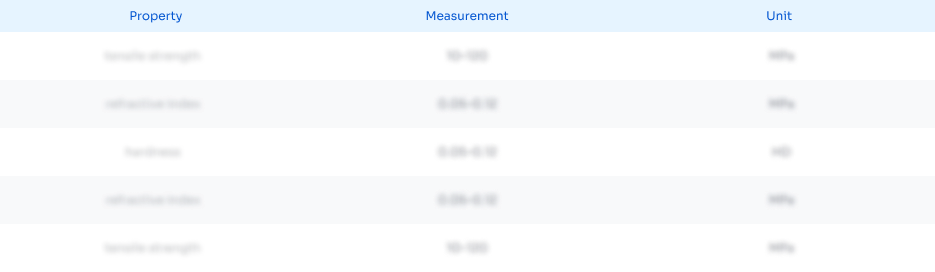
Abstract
Description
Claims
Application Information

- Generate Ideas
- Intellectual Property
- Life Sciences
- Materials
- Tech Scout
- Unparalleled Data Quality
- Higher Quality Content
- 60% Fewer Hallucinations
Browse by: Latest US Patents, China's latest patents, Technical Efficacy Thesaurus, Application Domain, Technology Topic, Popular Technical Reports.
© 2025 PatSnap. All rights reserved.Legal|Privacy policy|Modern Slavery Act Transparency Statement|Sitemap|About US| Contact US: help@patsnap.com