Method and arrangement in making of mechanical pulp
A mechanical pulping and pulping technology, applied in the regeneration of pulping liquid, textile and papermaking, fractionation/concentration of waste liquid, etc., to achieve the effect of improving cleanliness and reducing demand
- Summary
- Abstract
- Description
- Claims
- Application Information
AI Technical Summary
Problems solved by technology
Method used
Image
Examples
Embodiment Construction
[0044] By way of an example, Figure 1 illustrates the pulping process schematically. As shown in Figure 1, pulp is produced from a mechanical pulp, ie, fiber separation, such as from a mill 1 or refiner, generally at a consistency of about 0.1% to 0.8%. The mechanical pulp preparation process used can be, for example, thermomechanical pulping (TMP), grinding (GW / SGW; groundwood / groundwood), pressure grinding (PGW: pressure groundwood) or thermal grinding ( TGW; thermal groundwood pulp). The mechanical pulping process can also be chemi-thermomechanical pulping (CTMP) or chemi-mechanical pulping (CMP), which do not use bleaching agents in refining. By defibration, the pulp is introduced into a thickening 2, for example into a disc filter. During the thickening step the consistency of the pulp is generally raised to about 6-12% and the pulp is generally directed to intermediate storage 3 . The thickened filtrate is introduced into the white water tank 4, from where it is led b...
PUM
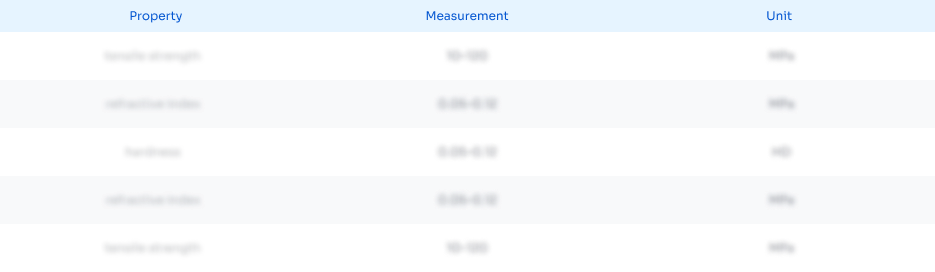
Abstract
Description
Claims
Application Information

- R&D Engineer
- R&D Manager
- IP Professional
- Industry Leading Data Capabilities
- Powerful AI technology
- Patent DNA Extraction
Browse by: Latest US Patents, China's latest patents, Technical Efficacy Thesaurus, Application Domain, Technology Topic, Popular Technical Reports.
© 2024 PatSnap. All rights reserved.Legal|Privacy policy|Modern Slavery Act Transparency Statement|Sitemap|About US| Contact US: help@patsnap.com