High-strength ceramsite proppant and preparation method thereof
A proppant, high-strength technology, applied in the field of preparation of the ceramsite proppant, can solve the problems of uneven particle size, low oil production rate, waste of resources, etc.
- Summary
- Abstract
- Description
- Claims
- Application Information
AI Technical Summary
Problems solved by technology
Method used
Examples
Embodiment 1
[0018] The ceramsite proppant of the present invention is made up of the component of following weight percentage content: Al 2 o 3 : 74%, SiO 2 : 10.5%, TiO 2 : 3.5%, Fe 2 o 3 : 9%, MnO 2 : 2.3%, K 2 O: 0.3%, Na 2 O: 0.1%, CaO: 0.2%, MgO: 0.1%. Wherein the raw material source of each component of the present invention is: Al 2 o 3 Derived from more than 72.5% Al 2 o 3 ore, MnO 2 Derived from manganese dioxide ore with a manganese dioxide content of 44-46%, SiO 2 From kaolin ore with a silica content of 20-25%, K 2 O, Na 2 O is taken from K 2 O content is 7.5%, Na 2 Potassium feldspar ore with 3.5% O content.
[0019] During preparation, the above raw materials are ground into fine powders above 325 mesh with an ultra-fine ray manganese mill and put into storage. The batching workshop mixes the above-mentioned fine powders in various proportions according to the components of the present invention, stirs for 40 minutes, and prepares To make a small sample mat...
Embodiment 2
[0021] The ceramsite proppant of the present invention is made up of the component of following weight percentage content: Al 2 o 3 : 78%, SiO 2 : 9.5%, TiO 2 : 2.5%, Fe 2 o 3 : 7%, MnO 2 : 2.0%, K 2 O: 0.4%, Na 2 O: 0.2%, CaO: 0.2%, MgO: 0.2%. Wherein the raw material source of each component of the present invention is: Al 2 o 3 Derived from more than 72.5% Al 2 o 3 ore, MnO 2 Derived from manganese dioxide ore with a manganese dioxide content of 44-46%, SiO 2 From kaolin ore with a silica content of 20-25%, K 2 O, Na 2 O is taken from K 2 O content is 7.5%, Na 2 Potassium feldspar ore with 3.5% O content.
[0022] During preparation, the above raw materials are ground into fine powders above 325 mesh with an ultra-fine ray manganese mill, and put into storage. The batching workshop mixes the above-mentioned fine powders in various proportions according to the composition of the components of the present invention, stirs for 50 minutes, and prepares To make...
Embodiment 3
[0024] The ceramsite proppant of the present invention is made up of the component of following weight percentage content: Al 2 o 3 : 80%, SiO 2 : 8.5%, TiO 2 : 3.5%, Fe 2 o 3 : 5%, MnO 2 : 1.9%, K 2 O: 0.4%, Na 2 O: 0.2%, CaO: 0.3%, MgO: 0.2%. Wherein the raw material source of each component of the present invention is: Al 2 o 3 Derived from more than 72.5% Al 2 o 3 ore, MnO 2 Derived from manganese dioxide ore with a manganese dioxide content of 44-46%, SiO 2 From kaolin ore with a silica content of 20-25%, K 2 O, Na 2 O is taken from K 2O content is 7.5%, Na 2 Potassium feldspar ore with 3.5% O content.
[0025] During preparation, the above raw materials are ground into fine powders above 325 mesh with an ultra-fine ray manganese mill, and put into storage. The batching workshop mixes the above-mentioned fine powders in various proportions according to the composition of the components of the present invention, stirs for 50 minutes, and prepares To make ...
PUM
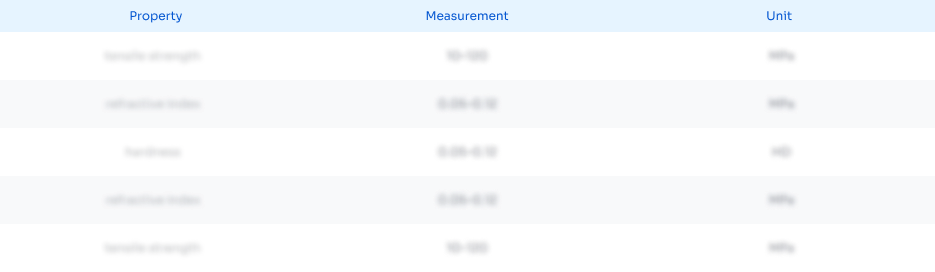
Abstract
Description
Claims
Application Information

- R&D Engineer
- R&D Manager
- IP Professional
- Industry Leading Data Capabilities
- Powerful AI technology
- Patent DNA Extraction
Browse by: Latest US Patents, China's latest patents, Technical Efficacy Thesaurus, Application Domain, Technology Topic, Popular Technical Reports.
© 2024 PatSnap. All rights reserved.Legal|Privacy policy|Modern Slavery Act Transparency Statement|Sitemap|About US| Contact US: help@patsnap.com