Process for decomposing bactnaesite by hydrochloric acid method
A technology of bastnaesite and process methods, applied in the fields of rare earth hydrometallurgy and bastnaesite smelting, can solve problems such as operational hazards and high alkali consumption, and achieve the goals of increasing the unit yield of equipment, increasing the yield of rare earths, and reducing costs Effect
- Summary
- Abstract
- Description
- Claims
- Application Information
AI Technical Summary
Problems solved by technology
Method used
Examples
Embodiment 1
[0023] 1) Bastnaesite concentrate is oxidized and roasted at 1000° C. for 2 hours to obtain bastnaesite mature ore with a cerium oxidation rate of 99%.
[0024] 2) Add water to bastnaesite mature ore, stir and adjust slurry, add solid sodium hydroxide, the weight ratio of sodium hydroxide to REO in the ore is 0.15:1, heat and keep warm at 80°C for 5 hours to obtain Alkali to mine.
[0025] 3) Add water to wash the alkali and transfer the ore to pH=7-8, and the temperature of the washing water is 50°C;
[0026] 4) Heat the alkali-converted pulp that has passed the water washing to 45°C, add 20% hydrochloric acid for optimal dissolution, add the acid for 3 hours, continue stirring for 0.5 hours, and separate the solid and liquid.
[0027] 5) In the excellent solution obtained in step 4), add qualified alkali-converted ore after washing with water, add barium chloride and ammonium sulfate, stir and react for 30 minutes, and separate solid and liquid. The weight ratio of barium ...
Embodiment 2
[0034] 1) The bastnaesite concentrate is oxidized and roasted at 350°C for 6 hours to obtain the bastnaesite mature ore with a cerium oxidation rate greater than 97.5%.
[0035] 2) Add water to bastnaesite cooked ore, stir and adjust the slurry, add solid sodium hydroxide, the weight ratio of sodium hydroxide to REO in the ore is 0.45:1, heat and keep warm at 120°C for 2 hours to obtain Alkali to mine.
[0036] 3) Add water to wash the alkali and transfer the ore to pH=7-8, and the temperature of the washing water is 95°C;
[0037] 4) Heat the alkali-converted pulp that has passed the washing process to 60°C, add 20% hydrochloric acid for optimal dissolution, add the acid for 3 hours, continue stirring for 3 hours, and separate the solid and liquid.
[0038] 5) In the excellent solution obtained in step 4), add qualified alkali-converted ore after washing with water, add barium chloride and ammonium sulfate, stir and react for 30 minutes, and separate solid and liquid. The w...
Embodiment 3
[0045] 1) The bastnaesite concentrate was oxidized and roasted at 800° C. for 6 hours to obtain bastnaesite mature ore with a cerium oxidation rate of 98.5%.
[0046] 2) Add water to bastnaesite cooked ore and stir to adjust the slurry, add solid sodium hydroxide, the weight ratio of sodium hydroxide to REO in the ore is 0.5:1, heat and react at 130°C for 0.5 hours to obtain Alkali to mine.
[0047] 3) Add water to wash the alkali and transfer the ore to pH=7-8, and the temperature of the washing water is 100°C;
[0048] 4) The temperature of the alkali-to-mineral pulp that has passed the water washing is 20°C, and 10% hydrochloric acid is added for optimal dissolution. The acid addition time is 1 hour, and the stirring is continued for 4 hours to separate the solid and liquid.
[0049] 5) In the excellent solution obtained in step 4), add qualified alkali-converted ore after washing with water, add barium chloride and ammonium sulfate, stir and react for 10 minutes, and sepa...
PUM
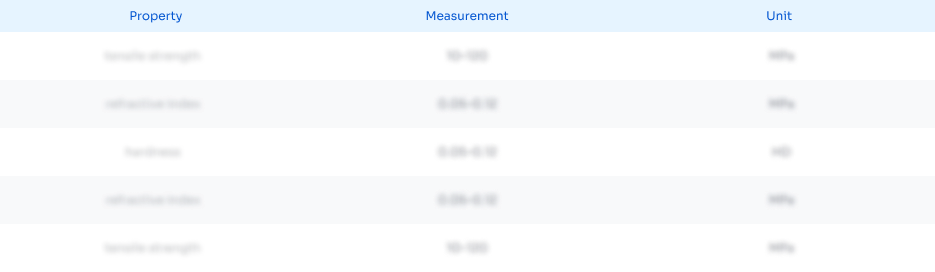
Abstract
Description
Claims
Application Information

- R&D Engineer
- R&D Manager
- IP Professional
- Industry Leading Data Capabilities
- Powerful AI technology
- Patent DNA Extraction
Browse by: Latest US Patents, China's latest patents, Technical Efficacy Thesaurus, Application Domain, Technology Topic, Popular Technical Reports.
© 2024 PatSnap. All rights reserved.Legal|Privacy policy|Modern Slavery Act Transparency Statement|Sitemap|About US| Contact US: help@patsnap.com