Concrete water reducing agent of polyacrylic acid and its synthesis process
A concrete water-reducing agent and a polyacrylic acid-based technology, which are applied in the field of polyacrylic-based high-efficiency water-reducing agent and synthesis technology, can solve the problems of complex production process of water-reducing agent and high equipment requirements, and achieve good appearance quality and anti-segregation performance. Good, no bleeding line effect
- Summary
- Abstract
- Description
- Claims
- Application Information
AI Technical Summary
Problems solved by technology
Method used
Image
Examples
Embodiment 1
[0051] Embodiment 1: Get the best matching ratio
[0052] Put 40.00 g of polyethylene glycol with a molecular weight of 400, 8.4 g of acrylic acid, 0.25 g of hydroquinone, 1.5 g of p-toluenesulfonic acid and 200 g of cyclohexane into a reaction vessel, stir at a temperature of 60° C. After diphenol and p-toluenesulfonic acid are completely dissolved, then keep the temperature at 80-90°C for 8 hours, then filter, vacuumize and remove cyclohexane to obtain polyethylene glycol monoacrylate; add 54.41g of water into a three-necked flask and The temperature is controlled at 85±5°C, and then 46.80g of the esterification product of the first step, 14g of acrylic acid and 9.16g of sodium 2-acrylamide-2-methylpropene sulfonate are added, and 54.41g of water is added to dissolve and mix until dripped. Dissolve 1.19 g of ammonium persulfate and 1.62 g of mercaptoethanol in 54.41 g, and add the three to the three-necked flask at a controlled rate dropwise, so that the drops are completed ...
Embodiment 2
[0054] Put 40.00g of polyethylene glycol with a molecular weight of 400, 10.5g of acrylic acid, 0.26g of hydroquinone, 2.65g of p-toluenesulfonic acid and 210g of cyclohexane into a reaction vessel, stir at a temperature of 60°C, and wait for p-toluenesulfonic acid to After diphenol and p-toluenesulfonic acid are completely dissolved, then keep the temperature at 80-90°C for 8 hours, then filter, vacuumize and remove cyclohexane to obtain polyethylene glycol monoacrylate; add 55.84 g of water into a three-necked flask and Control the temperature at 85±5°C, then add 46.80g of the first step esterification product, 14g of acrylic acid and 10.99g of sodium 2-acrylamide-2-methylpropene sulfonate, add 55.84g of water to dissolve and mix until dripping, then add water Dissolve 1.19 g of ammonium persulfate and 1.62 g of mercaptoethanol in 55.84 g, and add the three to the three-necked flask at a controlled rate dropwise, so that the drops are completed within 2 ± 0.5 hours, and the r...
Embodiment 3
[0056] Put 40.00g of polyethylene glycol with a molecular weight of 400, 8.4g of acrylic acid, 0.25g of hydroquinone, 1.51g of p-toluenesulfonic acid and 200g of cyclohexane into a reaction vessel, stir at a temperature of 60°C, and wait for p-toluenesulfonic acid to After the diphenol and p-toluenesulfonic acid are completely dissolved, then keep the temperature at 110-115°C and react for 8±0.5 hours, then filter, vacuumize and remove cyclohexane to obtain polyethylene glycol monomethacrylate; add 60.92g of water There is a three-necked flask and the temperature is controlled at 85±5°C, then add 46.80g of the esterification product of the first step, 22.36g of acrylic acid and 9.16g of sodium 2-acrylamide-2-methylpropenesulfonate, and add 60.92g of water to dissolve them Mix, dissolve 1.19 g of ammonium persulfate and 1.62 g of mercaptoethanol in 60.92 g of water, and add the three to the three-necked flask at a controlled rate dropwise, so that the drops are completed within ...
PUM
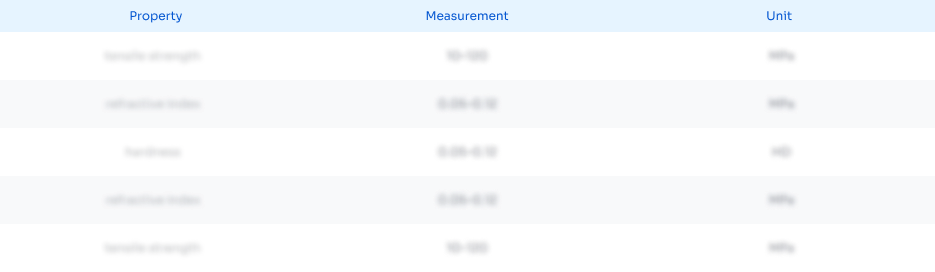
Abstract
Description
Claims
Application Information

- R&D
- Intellectual Property
- Life Sciences
- Materials
- Tech Scout
- Unparalleled Data Quality
- Higher Quality Content
- 60% Fewer Hallucinations
Browse by: Latest US Patents, China's latest patents, Technical Efficacy Thesaurus, Application Domain, Technology Topic, Popular Technical Reports.
© 2025 PatSnap. All rights reserved.Legal|Privacy policy|Modern Slavery Act Transparency Statement|Sitemap|About US| Contact US: help@patsnap.com