Method for producing magnesium-zirconium inter mediate alloy
A magnesium-zirconium master alloy and a production method technology are applied in the production field of magnesium-zirconium master alloy, which can solve the problems of polluted environment, difficult quality control, difficult operation and the like, and achieve the effects of simple production process, easy operation and improved product quality.
- Summary
- Abstract
- Description
- Claims
- Application Information
AI Technical Summary
Problems solved by technology
Method used
Examples
Embodiment 1
[0015] 1.1. Add metal magnesium and potassium salt KCL into the reduction furnace in a ratio of 1:1.5 by weight, start the vacuum system, stop vacuuming when the vacuum degree reaches 1Pa, and continuously feed argon as a protective gas. The pressure is +0.006MPa;
[0016] 1.2. According to the weight ratio of metal magnesium and zirconium tetrachloride 1:2, take zirconium tetrachloride and add it to the preheating furnace, start the vacuum system, when the vacuum degree reaches 6×10 -1 Pa, stop vacuuming, zirconium tetrachloride is heated, and through 2 hours, zirconium tetrachloride is heated to 330 ℃, zirconium tetrachloride is vaporized;
[0017] 1.3. While feeding the inert gas into the reduction furnace, heat the metal magnesium and potassium salt KCL. After 5 hours, heat the material to 950°C, and when the material reaches this temperature, introduce the vaporized zirconium tetrachloride into the reduction furnace. React with molten magnesium in the furnace for 8 hours...
Embodiment 2
[0019] 2.1. Add metal magnesium and potassium salt KF into the reduction furnace at a weight ratio of 1:0.9, start the vacuum system, and when the vacuum reaches 8×10 -1 Pa, stop vacuuming, and continuously feed argon as a protective gas, and the pressure in the furnace is +0.01MPa;
[0020] 2.2. According to the weight ratio of metal magnesium to zirconium tetrachloride 1:1.5, take zirconium tetrachloride and add it to the preheating furnace, start the vacuum system, when the vacuum degree reaches 4×10 -1 Pa, stop vacuuming, zirconium tetrachloride is heated, and through 5 hours, zirconium tetrachloride is heated to 600 ℃, zirconium tetrachloride is vaporized;
[0021] 2.3. While feeding the inert gas into the reduction furnace, heat the metal magnesium and potassium salt KF. After 3 hours, heat the material to 750°C, and when the material reaches this temperature, introduce the vaporized zirconium tetrachloride into the reduction furnace React with molten magnesium in the f...
Embodiment 3
[0023] 3.1. Add the mixture of metal magnesium and potassium salt KCL and KF into the reduction furnace in a weight ratio of 1:0.5, KCL:KF is a weight ratio of 3:1, start the vacuum system, when the vacuum reaches 5×10 -1 Pa, stop vacuuming, and continuously feed argon as a protective gas, and the pressure in the furnace is +0.02MPa;
[0024] 3.2. According to the ratio of metal magnesium to zirconium tetrachloride weight ratio of 1:1, take zirconium tetrachloride and add it to the preheating furnace, start the vacuum system, and stop vacuuming when the vacuum degree reaches 1Pa. Heating, after 4 hours, heating the zirconium tetrachloride to 500°C to vaporize the zirconium tetrachloride;
[0025] 3.3. While feeding the inert gas into the reduction furnace, heat the metal magnesium and potassium salt. After 2 hours, heat the material to 650°C, and when the material reaches this temperature, introduce the vaporized zirconium tetrachloride into the reduction furnace React with m...
PUM
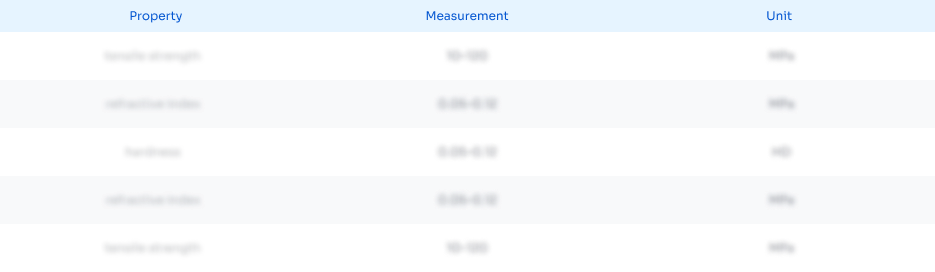
Abstract
Description
Claims
Application Information

- R&D Engineer
- R&D Manager
- IP Professional
- Industry Leading Data Capabilities
- Powerful AI technology
- Patent DNA Extraction
Browse by: Latest US Patents, China's latest patents, Technical Efficacy Thesaurus, Application Domain, Technology Topic, Popular Technical Reports.
© 2024 PatSnap. All rights reserved.Legal|Privacy policy|Modern Slavery Act Transparency Statement|Sitemap|About US| Contact US: help@patsnap.com