Contact hole shaping method, thin-membrane semiconductor producing method, electronic device and producing method thereof
A thin-film semiconductor and contact hole technology, used in semiconductor/solid-state device manufacturing, semiconductor devices, electrical components, etc., can solve the problems of high price, difficult to remove photoresist, long time, effort and energy, etc., to reduce costs , the effect of saving time and energy
- Summary
- Abstract
- Description
- Claims
- Application Information
AI Technical Summary
Problems solved by technology
Method used
Image
Examples
Embodiment Construction
[0034] Hereinafter, embodiments of the present invention will be described with reference to the drawings.
[0035] The method for forming a contact hole of the present invention and the best embodiment of an electronic device manufactured by the method will be described in detail with reference to the accompanying drawings.
[0036] figure 1 , figure 2 It is an example of the manufacturing process of the electronic device using the contact hole forming method of 1st Embodiment of this invention. This manufacturing process is a process using the contact hole forming method of the embodiment when forming a switching circuit such as a liquid crystal panel, and is a process diagram of a method of connecting a thin film transistor (TFT) made of low temperature polysilicon (LTPS) and wiring.
[0037] First, if figure 1 As shown in (1), an underlying insulating film 12 of silicon dioxide or the like is formed on the surface of the glass substrate 10 . The underlying insulating ...
PUM
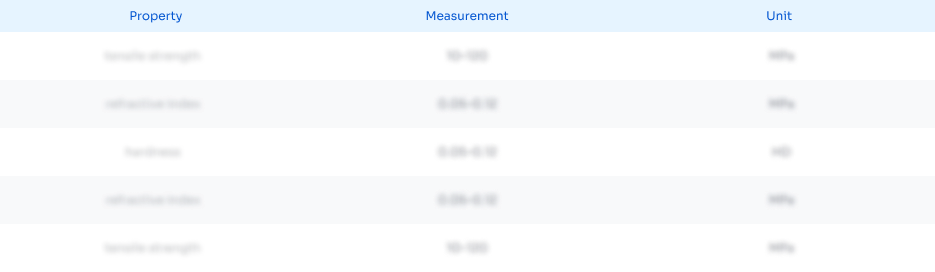
Abstract
Description
Claims
Application Information

- R&D
- Intellectual Property
- Life Sciences
- Materials
- Tech Scout
- Unparalleled Data Quality
- Higher Quality Content
- 60% Fewer Hallucinations
Browse by: Latest US Patents, China's latest patents, Technical Efficacy Thesaurus, Application Domain, Technology Topic, Popular Technical Reports.
© 2025 PatSnap. All rights reserved.Legal|Privacy policy|Modern Slavery Act Transparency Statement|Sitemap|About US| Contact US: help@patsnap.com