Whisker material modified polyurethane ground-paving material and preparation process thereof
A paving material and polyurethane technology, applied in the field of polyurethane floor paving materials and their preparation, can solve the problems of reducing the dispersibility of nano-montmorillonite in polyurethane, affecting the mechanical properties of polyurethane paving materials, etc., and achieve excellent semiconductor conductivity, Excellent antistatic properties and microwave absorption properties, improving stability and wear resistance
- Summary
- Abstract
- Description
- Claims
- Application Information
AI Technical Summary
Problems solved by technology
Method used
Examples
Embodiment 1
[0023] 1) Preparation of component A: Add 70% of polyether diol with a molecular weight of 2000 based on the total amount of component A into the reaction kettle, stir at 80-100°C, vacuumize and dehydrate for 1-3 hours, Cool to 40-60°C, add 30% diisocyanate, react at 70-90°C for 2-3 hours, vacuumize and degas, cool to room temperature for later use.
[0024] 2) Preparation of component B: take 40% of polyether triol with a molecular weight of 3000 based on the total amount of component B, vacuumize and dehydrate at 95-105°C for 1-3 hours, and add zinc oxide treated with coupling agent Whisker material 3%, ultrasonic treatment for 30 minutes in stirring state, add 3,3'-dichloro-4,4'diaminodiphenylmethane 4.0%, dioctyl phthalate 25%, talc powder 20% , 3% of silicon dioxide powder, 4.0% of iron red and 1% of lead naphthenate, stirred and mixed, heated to 80-95° C., vacuumed, dehumidified for 1-2 hours, cooled to room temperature for later use.
[0025] 3) Preparation of polyuret...
Embodiment 2
[0027] 1) Preparation of component A: Add 40% of polyether diol with a molecular weight of 2000 and 32% of polyether diol with a molecular weight of 1000 based on the total amount of component A into the reaction kettle, at 80-100°C Stir, vacuum dehydrate and degas for 1-3 hours, cool to 40-60°C, add 28% diisocyanate, react at 70-90°C for 2-3 hours, then vacuumize and degas, cool to room temperature for later use.
[0028] 2) Preparation of component B: Based on the total amount of component B, polyoxypropylene-refined castor oil polyol with a molecular weight of 3000 is 34%, vacuum dehydrated at 95-105°C for 1-3 hours, and treated with a coupling agent After 5% of the potassium hexatitanate whisker material was stirred and treated with ultrasonic waves for 40 minutes, 2.5% of 3,3'-dichloro-4,4'diaminodiphenylmethane and dioctyl phthalate were added 18%, kaolin 35%, silica powder 1%, tartrazine-phthalocyanine green 4.0% and lead isooctanoate 0.5%, stir and mix, heat up to 80-9...
Embodiment 3
[0031] 1) Preparation of component A: 34% of polyoxypropylene-refined castor oil polyol with a molecular weight of 2000 and 36% of polyether diol with a molecular weight of 1000 based on the total amount of component A were added to the reaction kettle, and at 80 Stir at -100°C, vacuum dehydrate and degas for 1-3 hours, cool to 40-60°C, add 30% diisocyanate, react at 70-90°C for 2-3 hours, then vacuumize and degas, cool to room temperature for later use .
[0032] 2) Preparation of component B: take 32% polyether triol with a molecular weight of 3000 based on the total amount of component B, dehydrate under vacuum at 95-105°C for 1-3 hours, add calcium sulfate treated with coupling agent Whisker material 5%, after ultrasonic treatment for 40 minutes under stirring, add 3,3'-dichloro-4,4'diaminodiphenylmethane 3.0%, chlorinated paraffin oil 26%, talcum powder 26%, di 3% of silicon oxide powder, 4.0% of iron red and 1% of lead naphthenate are stirred and mixed, heated to 80-95°...
PUM
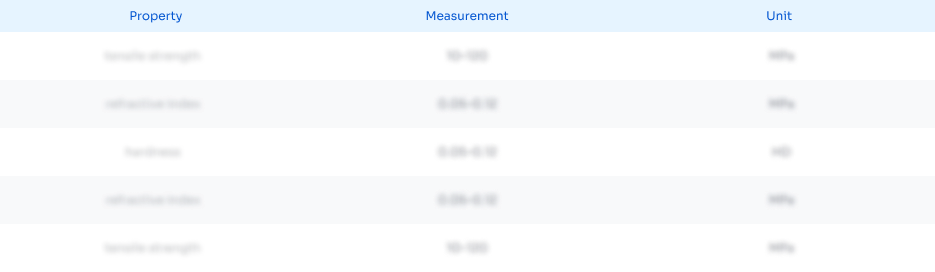
Abstract
Description
Claims
Application Information

- R&D Engineer
- R&D Manager
- IP Professional
- Industry Leading Data Capabilities
- Powerful AI technology
- Patent DNA Extraction
Browse by: Latest US Patents, China's latest patents, Technical Efficacy Thesaurus, Application Domain, Technology Topic, Popular Technical Reports.
© 2024 PatSnap. All rights reserved.Legal|Privacy policy|Modern Slavery Act Transparency Statement|Sitemap|About US| Contact US: help@patsnap.com