Composite polyol for producing hard polyurethane foam
A technology of combining polyol and rigid polyurethane, applied in the field of chemical materials, can solve the problems of increasing production cost, reducing production efficiency, prolonging demolding time, etc., and achieving the effects of saving production cost, improving production efficiency and excellent comprehensive performance
- Summary
- Abstract
- Description
- Claims
- Application Information
AI Technical Summary
Problems solved by technology
Method used
Examples
Embodiment Construction
[0025] Provide three specific embodiments below in conjunction with content of the present invention, the used raw material of the combination polyol formula involved:
[0026] (1) Polypropylene oxide / ethylene oxide polyether polyol with a molecular weight of 800 based on sucrose
[0027] (2) Polypropylene oxide polyether polyol with a molecular weight of 700 based on sorbitol
[0028] (3) Polypropylene oxide polyether polyol with a molecular weight of 150 based on ethylenediamine
[0029] (4) Polypropylene oxide polyether polyol with a molecular weight of 400 based on propylene glycol
[0030] (5) Polyester polyol with a molecular weight of 300 obtained by polycondensation of phthalic anhydride and polyol
[0031] (6) Glycerin
[0032] (7) water
[0033] (8) Catalyst: N, N-dimethylcyclohexylamine / pentamethyldiethylenetriamine=2 / 1
[0034] (9) Auxiliary material: dimethylpolysiloxane
[0035] components
[0036] Examples 1 to 3 show that when the combination ...
PUM
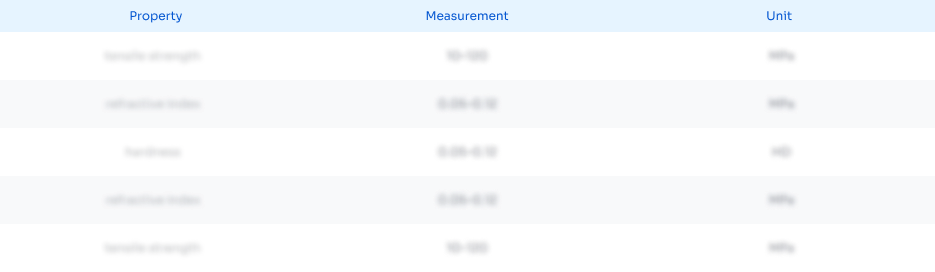
Abstract
Description
Claims
Application Information

- R&D
- Intellectual Property
- Life Sciences
- Materials
- Tech Scout
- Unparalleled Data Quality
- Higher Quality Content
- 60% Fewer Hallucinations
Browse by: Latest US Patents, China's latest patents, Technical Efficacy Thesaurus, Application Domain, Technology Topic, Popular Technical Reports.
© 2025 PatSnap. All rights reserved.Legal|Privacy policy|Modern Slavery Act Transparency Statement|Sitemap|About US| Contact US: help@patsnap.com