Catalyzer for catalyzing combustion and its preparing method
A catalytic combustion and catalyst technology, applied in the direction of catalyst activation/preparation, physical/chemical process catalysts, chemical instruments and methods, etc., can solve the problems of low utilization rate and uneven dispersion of noble metal components, and achieve good activity stability, The effect of uniform dispersion and high oxidation activity
- Summary
- Abstract
- Description
- Claims
- Application Information
AI Technical Summary
Problems solved by technology
Method used
Examples
Embodiment 1
[0018] Weigh 70g active γ-Al 2 o 3 Powder, 20g rutile TiO 2 powder, 5gCeO 2 powder, 5gZrO 2 Powder, mix evenly, add 4.0L distilled water, grind carefully to form an aqueous slurry. Immerse the cordierite honeycomb ceramic body in the above-mentioned water-containing slurry for 20 minutes, take it out, blow off the residual slurry in the hole with compressed air, dry it in the air at 120°C for 10 hours, and bake it in the air at 550°C for 3 hours. A coated honeycomb ceramic support. Then prepare the concentration of H containing 0.008gPt per milliliter of aqueous solution 2 PtCl 6 As for the aqueous solution, 30w% citric acid aqueous solution was added to make the concentration of citric acid in the mixed solution 0.5 mol / l, and the mixed solution was used as the impregnation solution for supporting the active component Pt. Immerse the prepared coated honeycomb ceramic carrier in the Pt impregnation solution for 120 minutes, take it out, dry it in the air at 100-120°C fo...
Embodiment 2
[0020] Weigh 50g active Al 2 o 3 Powder, 30g anatase TiO 2 powder, 15gCeO 2 powder, 5gZrO 2 Powder, mix evenly, add 2.0L distilled water, grind carefully to form a water-containing slurry. Immerse the cordierite honeycomb ceramic body in the above water-containing slurry for 40 minutes, then take it out, blow out the residual slurry in the hole with compressed air, dry it in the air at 120°C for 20 hours, and bake it in the air at 500°C for 5 hours, then it is produced A coated honeycomb ceramic support. Then prepare the concentration of H containing 0.004gPt per mL of aqueous solution 2 PtCl 6 As for the aqueous solution, 30w% oxalic acid aqueous solution is added to make the concentration of oxalic acid in the mixed solution 0.85 mol / l, and the mixed solution is used as the impregnation solution for loading the active component Pt. The prepared coated honeycomb ceramic carrier was immersed in the above Pt impregnation solution for 30 minutes, then taken out, dried in ...
Embodiment 3
[0022] Weigh 70g γ-Al 2 o 3 Powder, 14g Anatase TiO 2 powder, 10gCeO 2 Powder, 6gZrO2 Powder, mix well, add 1.4L of distilled water, grind carefully to form an aqueous slurry. Immerse the cordierite honeycomb ceramic body in the above-mentioned water-containing slurry for 30 minutes, take it out, blow off the residual slurry in the hole with compressed air, dry it in the air at 120°C for 12 hours, and bake it in the air at 550°C for 3 hours. A coated honeycomb ceramic support. Then prepare the concentration of H containing 0.008gPt per milliliter of aqueous solution 2 PtCl 6 Acetic acid was added to the aqueous solution so that the concentration of acetic acid in the mixed solution was 0.05 mol / l, and the mixed solution was used as the impregnation solution for supporting the active component Pt. The prepared coated honeycomb ceramic carrier was immersed in the above Pt impregnation solution for 60 minutes, then taken out, dried in air at 120°C for 20 hours, and calcined...
PUM
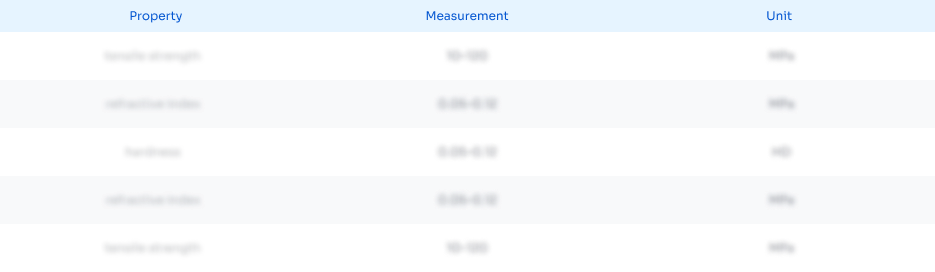
Abstract
Description
Claims
Application Information

- R&D
- Intellectual Property
- Life Sciences
- Materials
- Tech Scout
- Unparalleled Data Quality
- Higher Quality Content
- 60% Fewer Hallucinations
Browse by: Latest US Patents, China's latest patents, Technical Efficacy Thesaurus, Application Domain, Technology Topic, Popular Technical Reports.
© 2025 PatSnap. All rights reserved.Legal|Privacy policy|Modern Slavery Act Transparency Statement|Sitemap|About US| Contact US: help@patsnap.com