Polystyrene serial resin extruded foam plate and its producing method
A technology of polystyrene and a manufacturing method, which is applied in the field of extruded foam boards of polystyrene resins, can solve the problems of high thermal conductivity, high flammability of isobutane, difficulty in flame retardancy of foam, and achieve global warming. The effect of small coefficients
- Summary
- Abstract
- Description
- Claims
- Application Information
AI Technical Summary
Problems solved by technology
Method used
Image
Examples
Embodiment 1、3、4
[0093] Embodiment 1, 3, 4, comparative example 1, 2
[0094] As a raw material, 100 parts by weight of polystyrene (G330C manufactured by Toyo Styrene Co., Ltd.) was used as a talc masterbatch (composed of 69% by weight of the above-mentioned polystyrene and 30 parts by weight of talc (Hifira-#12 manufactured by Matsumura Sangyo Co., Ltd.)) as a cell regulator. % by weight and zinc stearate 1% by weight of zinc stearate) 16.7 parts by weight, 3 parts by weight of hexabromocyclododecane as a flame retardant and a mixture of a small amount of stabilizer and the amount shown in Table 1 (per 1 kg of polystyrene blowing agent injection amount (mol / kg)) in the ratio shown in Table 1 mixed with isobutane, methyl chloride, dimethyl ether, carbon dioxide blowing agent.
[0095] The extruder used was an extruder with a diameter of 65 mm (hereinafter referred to as "the first extruder"), an extruder with a diameter of 90 mm (hereinafter referred to as "the second extruder"), and an extru...
Embodiment 2
[0103] An extruded foam board was produced in the same manner as in Embodiment 1 except that the addition amount of the talc masterbatch was changed to 8.3 parts by weight. Table 2 shows the apparent density, thickness, independent cell ratio, average cell diameter in the thickness direction, cell deformation rate, thermal conductivity, flammability, and blowing agent remaining amount of the obtained extruded foam board.
PUM
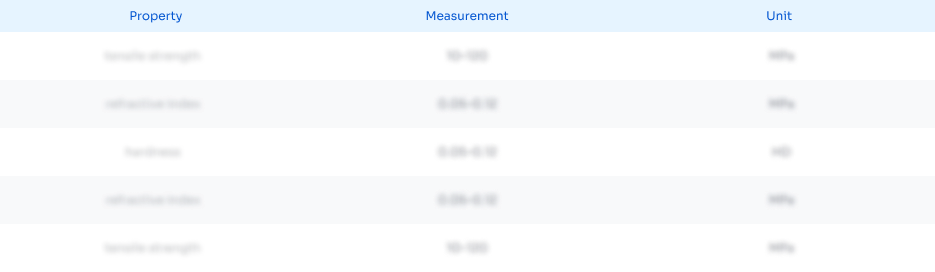
Abstract
Description
Claims
Application Information

- R&D
- Intellectual Property
- Life Sciences
- Materials
- Tech Scout
- Unparalleled Data Quality
- Higher Quality Content
- 60% Fewer Hallucinations
Browse by: Latest US Patents, China's latest patents, Technical Efficacy Thesaurus, Application Domain, Technology Topic, Popular Technical Reports.
© 2025 PatSnap. All rights reserved.Legal|Privacy policy|Modern Slavery Act Transparency Statement|Sitemap|About US| Contact US: help@patsnap.com