Carried siver catalyst for preparing anhydrous formaldehyde and its preparing process
An anhydrous formaldehyde, catalyst technology, applied in catalyst activation/preparation, chemical instruments and methods, physical/chemical process catalysts, etc., can solve the problems of no industrial application value, limited industrial application, no industrial prospect, etc. The effect of large-scale industrial production, insensitive reaction parameters, and easy production control
- Summary
- Abstract
- Description
- Claims
- Application Information
AI Technical Summary
Problems solved by technology
Method used
Examples
Embodiment 1
[0018] Embodiment 1: take by weighing 0.75g silver nitrate and be dissolved in 100mL water, add 5.56g Mg(NO 3 ) 2 ·6H 2 O, put it into a 250mL three-necked bottle after dissolving, add 33mL tetraethyl orthosilicate drop by drop, and at the same time vigorously electromagnetically stir, keep the oil bath temperature at 70°C, add 50mL of gelling agent ~ isopropanol, put it under reflux Condenser tube, after stirring for three hours, the sol solidified, stopped stirring, raised the temperature to 100°C, and evaporated the solvent for 12 hours. Transfer to a crucible, bake with an infrared lamp for 24 hours, then transfer to a muffle furnace and bake at 700°C for 6 hours, and crush it to 40-60 meshes to obtain Ag-SiO with a silver content of 5%. 2 -MgO catalyst, denoted as 1# catalyst.
Embodiment 2
[0019] Embodiment 2: take by weighing 1.5g silver nitrate and be dissolved in 100mL water, add 5.56g Mg(NO 3 ) 2 ·6H 2 O, put it into a 250mL three-neck bottle after dissolving, add 33mL tetraethyl orthosilicate at one time, and at the same time vigorously electromagnetically stir to maintain the temperature of the oil bath at 75°C, add 50mL of gelling agent ~ ethanol, and install a reflux condenser After stirring for six hours, the sol was solidified, the stirring was stopped, the temperature was raised to 90°C, and the solvent was evaporated for 24 hours. Transfer to a crucible, bake with an infrared lamp for 24 hours, then transfer to a muffle furnace for 10 hours at 650°C, and grind to 40-60 meshes to obtain Ag-SiO with a silver content of 10%. 2 -MgO catalyst, denoted as 2# catalyst.
Embodiment 3
[0020] Embodiment 3: take by weighing 2.25g silver nitrate and be dissolved in 100mL water, add 5.56g Mg(NO 3 ) 2 ·6H 2 Dissolve O, use 50mL ethanol as the gelling agent, and add a few drops of 1mol / L HNO 3 Auxiliary gelation, the same as example 2, Ag-SiO with a silver content of 15% can be obtained 2 -MgO catalyst, denoted as 3# catalyst.
PUM
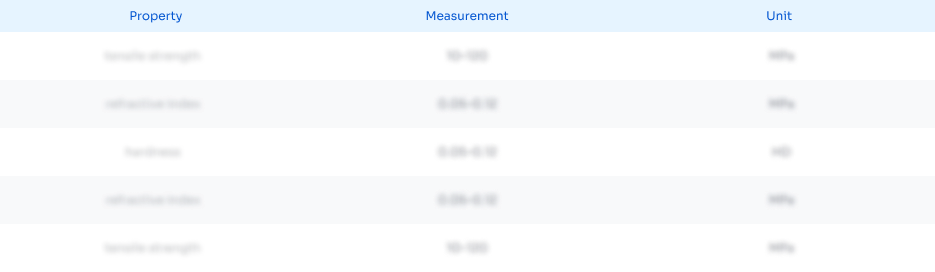
Abstract
Description
Claims
Application Information

- R&D
- Intellectual Property
- Life Sciences
- Materials
- Tech Scout
- Unparalleled Data Quality
- Higher Quality Content
- 60% Fewer Hallucinations
Browse by: Latest US Patents, China's latest patents, Technical Efficacy Thesaurus, Application Domain, Technology Topic, Popular Technical Reports.
© 2025 PatSnap. All rights reserved.Legal|Privacy policy|Modern Slavery Act Transparency Statement|Sitemap|About US| Contact US: help@patsnap.com