Ceramic and its making method
A manufacturing method and technology of ceramics, applied in the field of ceramics and its manufacturing, can solve the problems of damage to mechanical strength and particle characteristics and disadvantages of inorganic functional materials
- Summary
- Abstract
- Description
- Claims
- Application Information
AI Technical Summary
Problems solved by technology
Method used
Image
Examples
Embodiment 1
[0024] Hereinafter, embodiments of the present invention will be described with reference to the drawings. figure 1 Shown is an enlarged view of the internal structure of a flat ceramic as an example of the present invention. This ceramic is composed of inorganic functional material particles 1 and composite oxide particles 2 located between the innumerable inorganic functional material particles 1 . Such as figure 2 As shown, when the mixture 2a of inorganic compound particles containing at least one or more metal particles is mixed with the inorganic functional material powder 1a, it is fired, as figure 1 As shown, composite oxide particles 2 are formed between inorganic functional material particles 1 . In the figure, 3 represents a stomata.
[0025] Moreover, the manufacturing method of the ceramics of this invention has the following three steps.
[0026] For the formation of complex oxides 2, such as figure 2 As shown, a mixture 2a of at least two or more metal pa...
Embodiment 2
[0049] Hereinafter, a second embodiment of the present invention will be described. The composition of the ceramics used in Example 2 and its manufacturing method is omitted here because it is substantially the same as that of Example 1.
[0050] To form MgAl 2 o 4 It is a spinel composite oxide, and Al particles and MgO particles are mixed at a weight ratio of 57.3:42.7, and the mixed powder is used as a mixture of inorganic compound particles. 30 parts by weight of the mixture of inorganic compound fine particles and (100 parts by weight) of alumina powder were mixed, and fired at 1600° C. to obtain a ceramic (sample 21). Table 3 shows various properties of this sample including thermal conductivity.
[0051] Dimensional change rate (%)
Porosity (%)
Thermal conductivity (W / m·k)
Sample 21
0.0
9
18
Comparative sample 1
0.0
16
10
[0052] Here, Comparative Sample 1 is a ceramic using only Al particles as ...
Embodiment 3
[0055] Next, a third embodiment of the present invention will be described. The composition of the ceramics and its manufacturing method used in Example 3 is omitted here because it is substantially the same as that of Example 1.
[0056] To form Si 2 Al 6 o 13 It is a mullite (mullite) composite oxide. Al particles and Si particles are mixed at a weight ratio of 74.2:25.8, and the powder obtained after mixing is used as a mixture of inorganic compound particles. 30 parts by weight of the mixture of inorganic compound fine particles were mixed (per 100 parts by weight) of alumina powder, and fired at 1600° C. to obtain a ceramic (sample 22). Its properties including dielectric coefficient and thermal conductivity are shown in Table 4.
[0057] Dimensional change rate
(%)
Porosity (%)
(W / m·K)
Sample 22
-0.1
8
7.5
15
Comparative sample 1
0.0
16
9.8
10
...
PUM
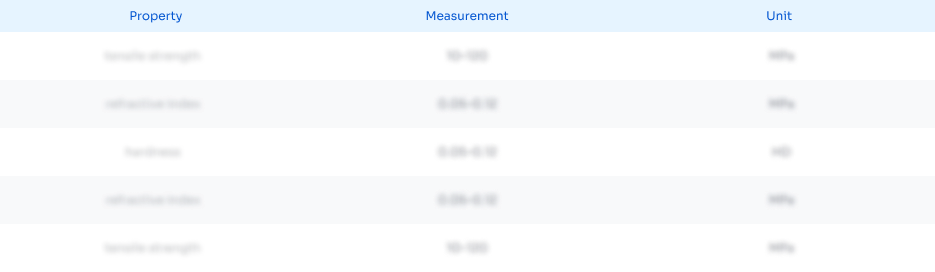
Abstract
Description
Claims
Application Information

- R&D Engineer
- R&D Manager
- IP Professional
- Industry Leading Data Capabilities
- Powerful AI technology
- Patent DNA Extraction
Browse by: Latest US Patents, China's latest patents, Technical Efficacy Thesaurus, Application Domain, Technology Topic, Popular Technical Reports.
© 2024 PatSnap. All rights reserved.Legal|Privacy policy|Modern Slavery Act Transparency Statement|Sitemap|About US| Contact US: help@patsnap.com