Alkali replenishing method during alumina production
A production process, alumina technology, applied in the preparation of alumina/aluminum hydroxide, alkali metal aluminate/alumina/aluminum hydroxide, etc., can solve the problem of inability to deal with alkali powder agglomeration, high labor intensity, affecting production and other problems, to achieve the effect of reducing the flying loss of alkali powder, optimizing the environment and saving human resources
- Summary
- Abstract
- Description
- Claims
- Application Information
AI Technical Summary
Problems solved by technology
Method used
Examples
Embodiment 1
[0013] A method for supplementing alkali in the alumina production process. The alkali liquor with an alkali content of 130g / l used in the preparation of raw slurry in conventional alumina production is introduced into a stirring container, and alkali powder is added to it and stirred to dissolve to a high degree. The lye with alkaline content, its Na 2 The concentration of O is 162.5g / l, and then it is sent into the lye storage tank with a slurry delivery pump to prepare raw slurry, and alkali is added to the conventional alumina production process along with the raw slurry, and the alkali content of the lye in the raw slurry is 136.9g / l.
Embodiment 2
[0015] The lye containing alkali concentration is 169g / l to introduce in a stirring container, and alkali powder is added therein and stirred and melted to obtain the lye with high alkali content, its Na 2 The concentration of O is 188.5g / l, and then it is sent into the lye storage tank with a slurry pump to prepare raw slurry, and the alkali is added to the conventional alumina production process along with the raw slurry, and the Na content of the raw slurry is 2 The concentration of O was 156.5 g / l.
Embodiment 3
[0017] The lye containing alkali concentration is 182g / l to introduce in a stirring container, and alkali powder is added therein and stirred and melted to obtain the lye with high alkali content, its Na 2 The concentration of O is 201.5g / l, and then it is sent into the lye storage tank with a slurry delivery pump to prepare raw slurry, and alkali is added to the conventional alumina production process along with the raw slurry, and the Na content of the raw slurry is 2 The concentration of O was 166.26 g / l.
PUM
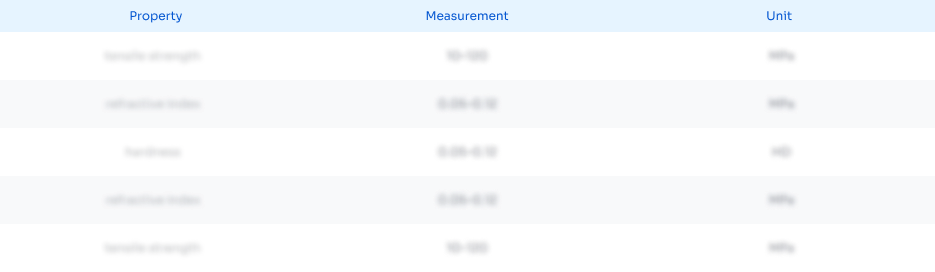
Abstract
Description
Claims
Application Information

- R&D
- Intellectual Property
- Life Sciences
- Materials
- Tech Scout
- Unparalleled Data Quality
- Higher Quality Content
- 60% Fewer Hallucinations
Browse by: Latest US Patents, China's latest patents, Technical Efficacy Thesaurus, Application Domain, Technology Topic, Popular Technical Reports.
© 2025 PatSnap. All rights reserved.Legal|Privacy policy|Modern Slavery Act Transparency Statement|Sitemap|About US| Contact US: help@patsnap.com