Improved method of preparing acrylic acid-2-ethyl caproite
A technology of ethylhexyl ester and acrylic acid, which is applied in the preparation of carboxylate, organic chemistry methods, chemical instruments and methods, etc., can solve the problems of interfering with distillation operations and reducing the environmental quality of production workshops.
- Summary
- Abstract
- Description
- Claims
- Application Information
AI Technical Summary
Problems solved by technology
Method used
Image
Examples
specific Embodiment approach
[0027] -Use 5-50% by weight of water based on the crude reaction mixture material (B1) to wash the crude reaction mixture (B1) with water; in addition, this step of washing the crude reaction mixture material (B1) with water is generally at a temperature of 20-50 at °C; and
[0028] - The hydrolysis is carried out at a temperature of 70-200°C.
Embodiment 1
[0030] The different logistics paths illustrated on FIGS. 1 and 2 have been described above. Embodiment 1 (the present invention)
[0031] A - Synthesis of Crude Reaction Mixture
[0032] In a stirred reactor, under reduced pressure and at a temperature of 90°C, in the presence of 94% sulfuric acid (9.76 parts) as a catalyst, and in the presence of phenothiazine (0.7 parts) as a polymerization inhibitor, 2-ethylhexyl Alcohol (520 parts) esterified acrylic acid (466.3 parts) in batch mode. The equilibrium of the esterification reaction is shifted towards the desired 2-ethylhexyl acrylate by distillation of the water produced as an azeotrope with 2-ethylhexanol.
[0033] The crude product (B1) of reaction is composed as follows:
[0034] 2-Ethylhexyl Acrylate 91%
[0035] 2-Ethylhexanol 4.4%
[0036] Acrylic acid 0.5%
[0037] 2-Ethylhexyl Acid Sulfate 2.5%
[0038] Water 0.5%
[0039] Other impurities 1.1%
[0040] B- Extract the catalyst by washing it three times with...
Embodiment 2
[0056] Embodiment 2 (comparison)
[0057] The process is carried out as described in conjunction with reference to FIG. 1 , which neutralizes the reaction crude product (b1) having the same composition as (B1). This process results in a thick emulsion during the neutralization step and also results in a loss of acrylic acid.
PUM
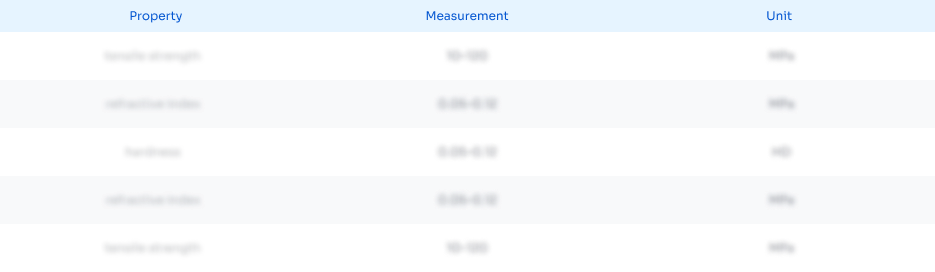
Abstract
Description
Claims
Application Information

- R&D Engineer
- R&D Manager
- IP Professional
- Industry Leading Data Capabilities
- Powerful AI technology
- Patent DNA Extraction
Browse by: Latest US Patents, China's latest patents, Technical Efficacy Thesaurus, Application Domain, Technology Topic, Popular Technical Reports.
© 2024 PatSnap. All rights reserved.Legal|Privacy policy|Modern Slavery Act Transparency Statement|Sitemap|About US| Contact US: help@patsnap.com