Rotor of small motor and its producing method
A manufacturing method and motor technology, applied in the manufacture of stator/rotor bodies, circuits, current collectors, etc., can solve problems such as inability to establish electrical connections, melting, difficult arc heat, etc.
- Summary
- Abstract
- Description
- Claims
- Application Information
AI Technical Summary
Problems solved by technology
Method used
Image
Examples
Embodiment Construction
[0020] Figure 4 The structure of the rotor of a small electric motor to which the present invention can be applied is shown in . The structure on the stator side is not shown here, but any suitable conventional structure may be used with the rotor. For example, a small motor can be installed by inserting the illustrated rotor into a hollow cylindrical metal case with a bottom, relying on two magnets on its inner peripheral surface; installing the case cover to cover the opening of the metal case end. In this way, the two ends of the rotor shaft 11 are supported by two bearings, one bearing is arranged at the center of the bottom of the casing, and the other is arranged on the casing cover. Usually, a brush supported by the housing cover is also provided, and when the brush is in sliding contact with the commutator of the rotor, it is connected to the input terminal that enters the housing cover and protrudes inside to provide electrical energy from the outside .
[0021] ...
PUM
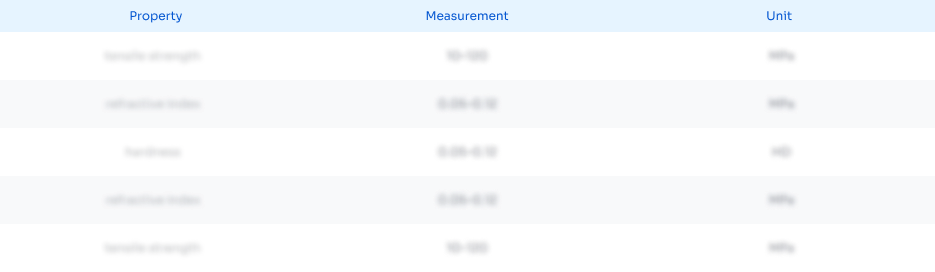
Abstract
Description
Claims
Application Information

- Generate Ideas
- Intellectual Property
- Life Sciences
- Materials
- Tech Scout
- Unparalleled Data Quality
- Higher Quality Content
- 60% Fewer Hallucinations
Browse by: Latest US Patents, China's latest patents, Technical Efficacy Thesaurus, Application Domain, Technology Topic, Popular Technical Reports.
© 2025 PatSnap. All rights reserved.Legal|Privacy policy|Modern Slavery Act Transparency Statement|Sitemap|About US| Contact US: help@patsnap.com