Production method of non-convertible combined methanol and dimethyl ether from coke oven gas
A production method and technology of dimethyl ether, applied in the field of coking enterprises, can solve the problems of high energy consumption, large investment and high cost of dimethyl ether production
- Summary
- Abstract
- Description
- Claims
- Application Information
AI Technical Summary
Problems solved by technology
Method used
Image
Examples
Embodiment Construction
[0006] The specific embodiments of the present invention will be described in detail below in conjunction with the production process flow chart.
[0007] As shown in Figure 1, the production method of the present invention is that the coke oven gas (ie raw material gas) enters the Roots blower 2 through the raw gas tank 1, and the gas after the Roots blower passes through the coarse desulfurization tower 3 and the fine desulfurization tower 4 to be removed. Sulfur and ammonia harmful components and gases are compressed by compressor 5 and sent to methanol synthesis tower 6 at 3.0-5.0Mpa, where the copper-based catalyst (C u ), the temperature is 220℃-300℃, the pressure is 3.0-5.0Mpa, in the methanol synthesis tower 6, the coke oven gas part H 2 And CO and CO 2 The reaction produces methanol, and the hot mixed gas after methanol is fed into the dimethyl ether synthesis tower 7 at a temperature of 200-280°C, where the modified alumina catalyst (Al 2 O 3 ) Under the action of the te...
PUM
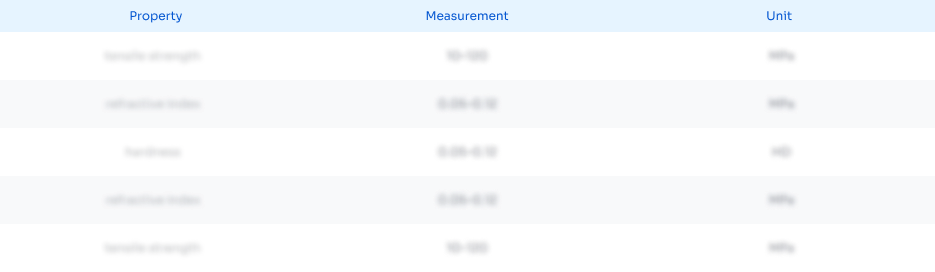
Abstract
Description
Claims
Application Information

- R&D
- Intellectual Property
- Life Sciences
- Materials
- Tech Scout
- Unparalleled Data Quality
- Higher Quality Content
- 60% Fewer Hallucinations
Browse by: Latest US Patents, China's latest patents, Technical Efficacy Thesaurus, Application Domain, Technology Topic, Popular Technical Reports.
© 2025 PatSnap. All rights reserved.Legal|Privacy policy|Modern Slavery Act Transparency Statement|Sitemap|About US| Contact US: help@patsnap.com