Process for extrusion casting piston blank of internal combustion engine with local reinforced of metal base composite material
A composite material and local enhancement technology, applied in the directions of pistons, rotors, cylinders, etc., can solve the problems of human mucous membranes and environmental protection, poor slag discharge in the cavity, etc. Effect
- Summary
- Abstract
- Description
- Claims
- Application Information
AI Technical Summary
Problems solved by technology
Method used
Examples
Embodiment 1
[0064] The process of partially reinforcing the piston blank of an internal combustion engine by the squeeze casting metal matrix composite material of this embodiment adopts the following steps:
[0065] (1) Making reinforced phase pre-components
[0066] Using metal matrix composite material reinforced phase pre-component preparation method, metal matrix composite material local reinforced product pre-component preparation method, short fiber reinforced metal matrix composite product porous preform preparation method to make reinforced phase pre-component, metal matrix composite material reinforced The preparation method of the phase pre-component has been recorded in the Chinese patent application number 03134444.5, and the preparation method of the metal matrix composite material partial reinforcement product pre-component has been described in the Chinese patent application number 03134445.3. Short fiber reinforced metal matrix composite The preparation method of the porous p...
Embodiment 2
[0099] In this embodiment, in the process step of (2) preparing the base alloy charge, the base alloy charge is prepared according to the following weight ratio:
[0100] Silicon 11%
[0101] Copper 0.5%
[0102] Magnesium 0.4%
[0103] Manganese 0.2%
[0104] Vanadium 0.05%
[0105] Aluminum up to 100%
[0106] In (5) the modification treatment process step, in the alloy melt, add the following ternary composite modifier (based on the added amount of single element) that is crushed to 5-10mm particles by weight percentage of the base alloy charge:
[0107] Be 0.013%
[0108] Ti 0.04%
[0109] Te 0.002%
[0110] The other process steps are the same as in Example 1.
Embodiment 3
[0112] In this embodiment, in the process step of (2) preparing the base alloy charge, the base alloy charge is prepared according to the following weight ratio:
[0113] Silicon 13%
[0114] Copper 2.0%
[0115] Magnesium 1.4%
[0116] Manganese 0.9%
[0117] Vanadium 0.27%
[0118] Aluminum up to 100%
[0119] In (5) the modification treatment process step, in the alloy melt, add the following ternary composite modifier (based on the added amount of single element) that is crushed to 5-10mm particles by weight percentage of the base alloy charge:
[0120] Be 0.016%
[0121] Ti 0.06%
[0122] Te 0.004%
[0123] The other process steps are the same as in Example 1.
PUM
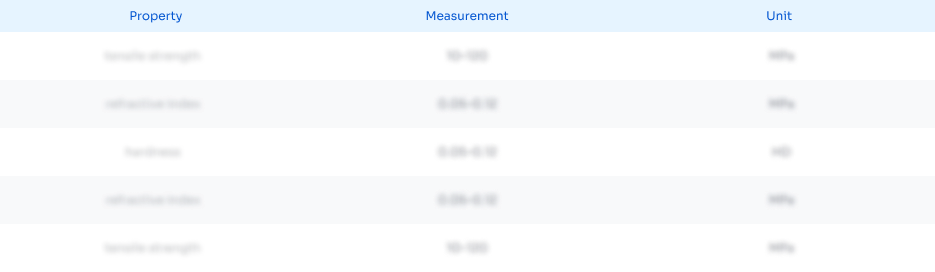
Abstract
Description
Claims
Application Information

- R&D Engineer
- R&D Manager
- IP Professional
- Industry Leading Data Capabilities
- Powerful AI technology
- Patent DNA Extraction
Browse by: Latest US Patents, China's latest patents, Technical Efficacy Thesaurus, Application Domain, Technology Topic, Popular Technical Reports.
© 2024 PatSnap. All rights reserved.Legal|Privacy policy|Modern Slavery Act Transparency Statement|Sitemap|About US| Contact US: help@patsnap.com