Collagen protein-polyacrylonitrile composite fiber and its preparation method
A technology of collagen and polyacrylonitrile, applied in the direction of conjugated synthetic polymer artificial filament, cellulose/protein conjugated artificial filament, etc., can solve the problems of slow degradation speed, environmental pollution, etc., and achieve improved strength and elongation , to avoid fiber brittleness, not easy to play the effect of static electricity
- Summary
- Abstract
- Description
- Claims
- Application Information
AI Technical Summary
Problems solved by technology
Method used
Image
Examples
Embodiment 1
[0032] Take the raw hides after dehairing and liming, put them in the meat remover, cut them into 2cm×2cm pieces, put them in the drum, wash them with 3 times of 35°C water for 15 minutes, control the water and then wash them again, pour them out. After removing the water in the drum, add 3 times of 35°C water, 2% ammonium sulfate and 0.5% equal weight of the bark, rotate for 40 minutes, discard the water in the drum, and use 3 times of 35°C clean water. Wash twice with water and control to dry, transfer the washed skin to the reaction kettle, add 2 times of water, gradually heat up to 80 ° C, and keep the temperature for 6 hours to gradually dissolve the raw skin, filter, take the filtrate and adjust the concentration to 14wt%.
[0033] Analyze the concentration of collagen solution, transfer 100Kg collagen solution to the reaction kettle, heat it up to 50°C, add 126Kg ZnCl 2 , stir to dissolve it completely, add 0.21Kg of ammonium persulfate dissolved in water (1.5% of the w...
Embodiment 2
[0038] Take the tannery's gray skin and discarded shavings, put it in the drum, wash it with 3 times of 35 ℃ water for 15 minutes, control the water and then wash it again, pour out the water in the drum, add 3 Add water at 35°C, 2% ammonium sulfate and 0.5% ammonium sulfate by weight of the bark, rotate for 40 minutes, discard the water in the drum, wash twice with 3 times the water at 35°C and control to dry, transfer the bark In the reaction kettle, add 3 times of water, gradually heat up to 80 ° C, and keep the temperature for 4 hours to gradually dissolve the dandruff. After filtration, the filtrate is collected, concentrated and spray-dried to obtain collagen solid powder.
[0039] The collagen solid powder was dissolved in dimethyl sulfoxide to obtain a collagen solution with a concentration of 6 wt%, which was transferred to a reaction kettle, heated to 68 ° C, and dissolved in dimethyl sulfoxide into an azo of 0.5% by weight of collagen. Diisobutyronitrile was gradual...
Embodiment 3
[0044] The gelatin solid was dissolved in ethyl carbonate to obtain a collagen solution with a concentration of 15wt%, which was transferred to a reaction kettle, heated to 75°C, and dissolved into benzoyl peroxide of 1% by weight of collagen with ethyl carbonate. It was added to the reaction kettle, and 40% acrylonitrile, 5% acrylamide and 15% ethyl acrylate mixed monomers by weight of collagen were simultaneously added dropwise. Sexual collagen solution.
[0045] The polyacrylonitrile solid was added to ethyl carbonate, stirred under heating, and the polyacrylonitrile was completely dissolved to obtain a polyacrylonitrile solution with a concentration of 15%;
[0046] Mix the above two solutions in proportion, the weight of the modified collagen solution is 20 parts, and the weight of the polyacrylonitrile solution is 80 parts, stir at 90 ° C for 1 hour, and stand at 80 ° C for 6 hours under normal pressure for defoaming . The spinning stock solution after defoaming is fil...
PUM
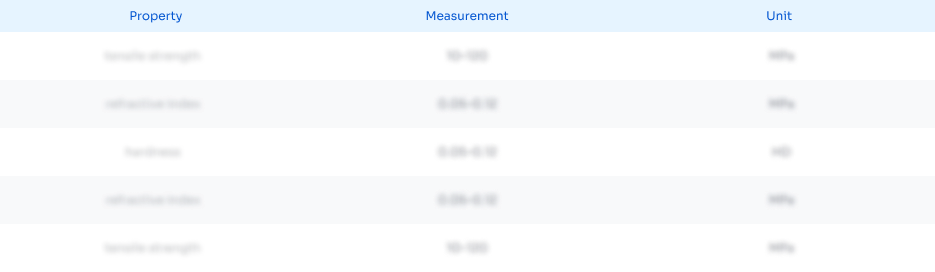
Abstract
Description
Claims
Application Information

- R&D
- Intellectual Property
- Life Sciences
- Materials
- Tech Scout
- Unparalleled Data Quality
- Higher Quality Content
- 60% Fewer Hallucinations
Browse by: Latest US Patents, China's latest patents, Technical Efficacy Thesaurus, Application Domain, Technology Topic, Popular Technical Reports.
© 2025 PatSnap. All rights reserved.Legal|Privacy policy|Modern Slavery Act Transparency Statement|Sitemap|About US| Contact US: help@patsnap.com