Preparation process of active zironium white pigment
A kind of pigment and active technology, which is applied in the field of preparation of active zirconium white pigments, can solve the problems of not being able to be used as paint pigments, easy to change color of exterior wall coatings, not being compatible with resins and mixing, etc., to achieve excellent weather resistance and anti-aging performance, unique Absorption and shielding effect, effect of small thermal expansion coefficient
- Summary
- Abstract
- Description
- Claims
- Application Information
AI Technical Summary
Problems solved by technology
Method used
Examples
Embodiment 1
[0023] a. stirring and grinding
[0024] Choose zirconium silicate (ZrO in zirconium silicate 2 ·SiO2 2 ≥99%, of which ZrO 2 ≥65.5%, SiO 2 ≤33.5%) as base material, add grinding aid sodium carbonate and tap water, press 100: 0.3: 130 weight ratio, make ZJM-120 type agitating ball mill with Zhengzhou City Dongfang Machinery Manufacturing Factory and grind under stirring wheel speed 80 rpm 9 hours to an average particle size of 1.2-1.3 μm, the diameter of zirconium balls or high alumina balls is 6 mm, and the total weight ratio of grinding balls to materials plus water is equal to 1:1.4;
[0025] b. Rinsing, magnetic filtration to remove iron and press filter dehydration
[0026] Rinse the slurry obtained by stirring and grinding with well water twice the weight of the slurry, pass through a 400-mesh cylindrical sieve to remove impurities, and pass the slurry evenly through the HI-100 magnetic filter to remove iron; use XMT60 / 800-UB type filter press filter dehydration to ...
Embodiment 2
[0036] Similar to the preparation method in Example 1, the difference is that zirconium oxide is used instead of zirconium silicate as the base material, and in step a, it is ground with a ZJM-120 type agitating ball mill from Zhengzhou Dongfang Machinery Manufacturing Plant at a stirring wheel speed of 100 rpm Between 12 hours to an average particle size of 0.3-0.5 μm; c. the weight ratio of the cake to sodium hypophosphite and magnesium oxide powder in the step is 100: 0.2: 0.3; after the calcined material is cooled in the e step, use a hammer mill Thin, mix with the plating solution of 6.0% powder weight, the weight ratio of strontium chloride, sodium hypophosphite, dehydrated alcohol and simethicone oil in the plating solution is 15: 10: 25: 100, and the airflow pressure is 1.0Mpa (MPa ), the coating reaction temperature is 95°C, and the speed of the zirconium sheet classification wheel is 4800 rpm.
[0037] The prepared active zirconium white pigment has the excellent pro...
Embodiment 3
[0039] Similar to the preparation method in Example 1, the difference is that the mixture of 30 parts by weight of zirconium oxide and 70 parts by weight of zirconium silicate is used as the base material, and the ZJM-120 type agitating ball mill of Zhengzhou Dongfang Machinery Manufacturing Plant is used to stir in step a. Grinding for 10 hours at a wheel speed of 80 rpm to an average particle size of 0.8-1.0 μm; c. the weight ratio of the cake to sodium hypophosphite and magnesium oxide powder in the step is 100: 0.4: 0.6; d. the mixture in the step Heating and calcining at 200-560°C for 4 hours, then gradually heating up to 1200°C for high-temperature calcining for 5 hours; e. the amount of plating solution in the step is 4.8% of the powder weight, strontium chloride, sodium hypophosphite, absolute ethanol and di The weight ratio of methyl silicone oil is 25:10:20:100, the gas flow pressure is 0.9Mpa (MPa), the coating reaction temperature is 85°C, the pH value is 6.5, and t...
PUM
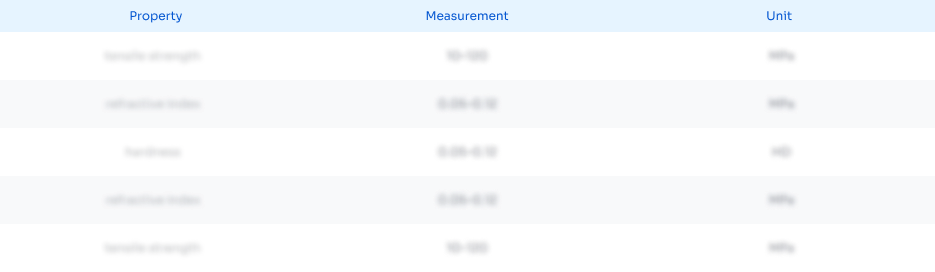
Abstract
Description
Claims
Application Information

- R&D
- Intellectual Property
- Life Sciences
- Materials
- Tech Scout
- Unparalleled Data Quality
- Higher Quality Content
- 60% Fewer Hallucinations
Browse by: Latest US Patents, China's latest patents, Technical Efficacy Thesaurus, Application Domain, Technology Topic, Popular Technical Reports.
© 2025 PatSnap. All rights reserved.Legal|Privacy policy|Modern Slavery Act Transparency Statement|Sitemap|About US| Contact US: help@patsnap.com