Continuous induction heat treatment process for high-strength finish-rolled spiral steel bar
A technology of induction heat treatment and finish rolling of threads, applied in heat treatment furnaces, heat treatment equipment, improvement of process efficiency, etc., can solve the problems of coarse grains in the center, unstable performance of steel bars, shallow hardening layer, etc., and achieve fine grains. The effect of good matching of strength and toughness, and high strength level
- Summary
- Abstract
- Description
- Claims
- Application Information
AI Technical Summary
Problems solved by technology
Method used
Examples
Embodiment Construction
[0011] According to the continuous heat treatment process provided by the present invention, the chemical composition by weight percentage is: C: 0.40-0.60%, Si: 0.60-2.0%, Mn: 0.60-2.0%, Mo: 0.10-0.40%, V: 0.10-0.30 %, P, S≤0.03% of the finished rolled threaded steel bar is automatically uploaded to the conveying roller table from the feeding system of the continuous heat treatment device, and the steel bar is heated by an induction heater at a speed of 2-6 m / min in a rotating state. Heating the steel bars to 820-980°C, and then enter the cooler for quenching treatment, after quenching, the temperature is lower than 300°C, and then enter the next induction heater for tempering heat treatment, the tempering temperature is 580-680°C, after the above continuous After the heat treatment process, the finished rolled threaded steel bar with a strength level of 800MPa is obtained. Finally, it is automatically sent to the unloading system and enters the finished product collection ta...
PUM
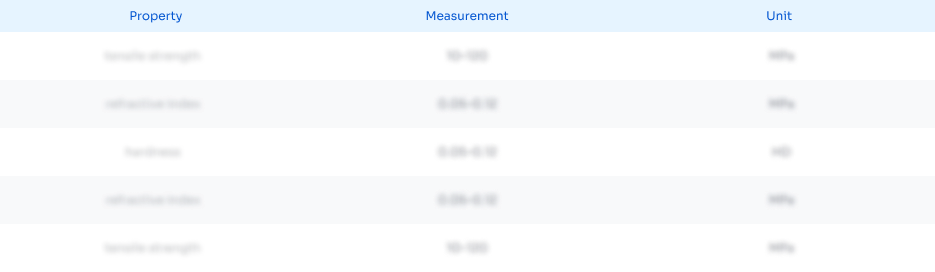
Abstract
Description
Claims
Application Information

- R&D
- Intellectual Property
- Life Sciences
- Materials
- Tech Scout
- Unparalleled Data Quality
- Higher Quality Content
- 60% Fewer Hallucinations
Browse by: Latest US Patents, China's latest patents, Technical Efficacy Thesaurus, Application Domain, Technology Topic, Popular Technical Reports.
© 2025 PatSnap. All rights reserved.Legal|Privacy policy|Modern Slavery Act Transparency Statement|Sitemap|About US| Contact US: help@patsnap.com